Технология монтажа электрических машин и средств автоматизации
3.3.1 Технология монтажа электрических машин
3.3.1.1 Электрические машины
3.3.1.2 Технология монтажа электрических машин прибывающих с заводов изготовителей в собранном виде
3.3.1.3 Технология монтажа электрических машин прибывающих с заводов изготовителей в разобранном виде
3.3.1.4. Технология монтажа взрывозащищенных электродвигателей
3.3.2. Технология монтажа средств автоматизации
3.3.1 Технология монтажа электрических машин
3.3.1.1 Электрические машины
Электрические машины классифицируют по роду тока, мощности, степени защиты, способу охлаждения, конструктивному исполнению и способу монтажа.
По роду тока электрические машины разделяют на машины постоянного и переменного тока.
По мощности электрические машины делят на машины малой мощности до 100 кВт, средней –100-1000 кВт и большой – выще 1000 кВт.
По степени защиты электрические машины классифицируют на следующие группы: защиты персонала от соприкосновения с токоведущими или вращающимися частями, находящимися внутри машины; защиты от попадания внутрь машины твердых посторонних тел и воды.
По способу охлаждения электрические машины разделяют на машины с естественным и искусственным охлаждением.
По конструктивному исполнению и способу монтажа электрические машины делят на девять групп: 1М1 – на лапах с подшипниковыми щитами с пристроенным редуктором;
1М2 – на лапах с подшипниковыми щитами, с фланцем на подшипниковом щите;
1М3 – без лап с подшипниковыми щитами, с фланцем на одном подшипниковом щите, с кольцевым фланцем;
1М4 –без лап с подшипниковыми щитами, с фланцем на станине;
1М5 – без подшипниковых щитов (встраиваемые или пристраиваемые);
1М6 –на лапах с подшипниковыми щитами и стояковыми подшипниками;
1М7 –на лапах со стояковыми подшипниками (без подшипниковых щитов);
1М8 –с вертикальным валом;
1М9 –специального назначения.
Наиболее распространенными электрическими машинами являются асинхронные. Асинхронной называют машину переменного тока, частота вращения ротора которой зависит от нагрузки. Магнитное поле в асинхронной машине создается переменным током обмоток статора и ротора. Частота вращения ротора отличается от частоты вращения магнитного поля статора. Асинхронные машины по конструктивным признакам подразделяют на машины с короткозамкнутым ротором и фазным ротором.
Основным типом асинхронной машины является трехфазный асинхронный двигатель с короткозамкнутым ротором (рис. 3.39) и асинхронный двигатель с фазной обмоткой ротора (рис. 3.40). Для уменьшения вихревых токов сердечники статора и ротора набирают из листов электротехнической стали толщиной 0,35 или 0,5 мм, изолированных один от другого слоем лака или оксидной пленкой. Основная серия асинхронных двигателей 4А включает машины мощностью 0,4–400 кВт.
Асинхронные электродвигатели единой серии мощностью свыше 400 кВт, выпускают на напряжение свыше 1000 В.
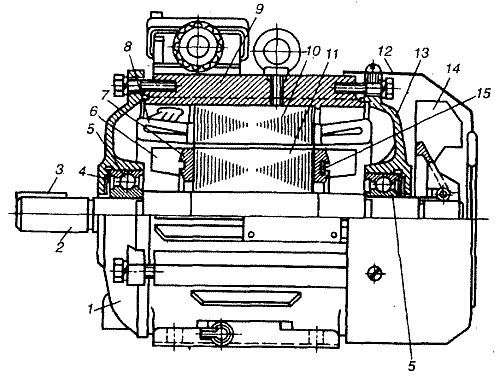 Рис. 3.39. Асинхронный электродвигатель единой серии 4А: 1, 13– передний и задний щиты, 2 – вал, 3 – шпонка, 4 – установочная пружина, 5 – подшипник, 6 – крыльчатка, 7 – короткозамыкающие кольца, 8 – лобовая часть обмотки статора, 9 – станина, 10, 11 – сердечники статора и ротора, 12 – кожух вентилятора, 14 – вентилятор, 15 – балансировочный грузик.
Асинхронные машины с фазным ротором используют в качестве двигателей, но они имеют ограниченное применение. Как правило, они применяются для привода механизмов по технологии, которых предусмотрено регулирование частоты вращения.
Машину переменного тока, ротор которой вращается с частотой, равной частоте вращения магнитного поля, созданного обмоткой статора, включенной в электрическую сеть, называют синхронным электродвигателем. По конструктивному исполнению все синхронные машины делят на явнополюсные и неявнополюсные. Явнополюсные машины изготовляют на диапазон частот вращения от нескольких десятков до 1500 об/мин, неявнополюсные – на 3000 об/мин. Конструкция синхронных генераторов аналогична конструкции синхронных двигателей. Работа синхронных генераторов основана на принципе электромагнитной индукции. Если через неподвижные щетки, скользящие по двум вращающимся кольцам, к обмоткам полюсов подвести постоянный ток Iв, он создает магнитный поток. Силовые линии этого потока будут замыкаться через полюса и сердечник статора, в пазы которого закладывается обмотка. При вращении намагниченных полюсов ротора, осуществляемом от турбины, магнитный поток ротора, пересекая обмотку статора, будет
индуцировать в ней ЭДС. Так как обмотка статора пересекается магнитным потоком,
который изменяет при вращении полюсов свое направление, то индуцируемая ЭДС
будет переменной. Чем больше частота вращения, тем больше ЭДС. С увеличением частоты
вращения размеры и масса синхронных генераторов уменьшаются.
Промышленность изготовляет двухполюсные генераторы мощностью 2,5; 4; 6; 12; 30; 50; 60; 100; 150; 200; 300; 500; 800 и 1200 МВт.
Трехфазные синхронные машины мощностью 320–10000 кВт объединены в единую серию машин 14-20-го габаритов совместно с асинхронными двигателями. Такое объединение позволяет многие части машин (сборочные единицы), например, статоры, подшипниковые стояки, фундаментные плиты, выполнять одинаковыми для синхронных и асинхронных двигателей и получать значительную экономию трудозатрат при их совместном производстве.
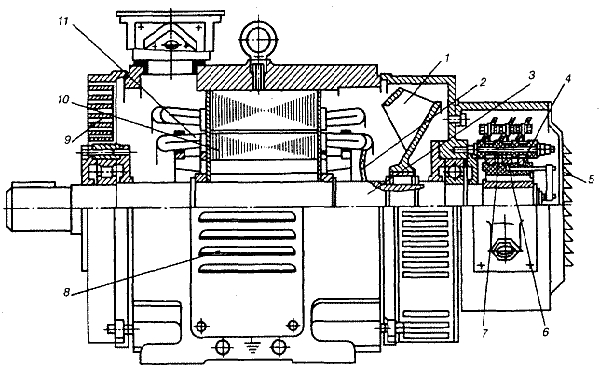 Рис. 3.40. Асинхронный двигатель с фазным ротором: 1 – вентилятор, 2 – вывод роторной обмотки, 3,11 –вал и обмотка ротора, 4 – контактные кольца, 5 – крышка, 6 – щетки, 7–щеткодержатели, 8 – жалюзи, 9 – щит, 10 – ротор.
Синхронный генератор, сердечник 6 статора которого стянут шпильками 7 в неразъемном сварном корпусе 5, показан на рис. 3.41. В открытые пазы вложены катушки обмотки 8 статора; их лобовые части защищены кожухом 4.
Крестовина ротора 11 сварная. К ободу крестовины болтами прикреплены полюсы 9 с надетыми на них катушками обмоток возбуждения и вентиляторные лопатки 10. Выводы от обмоток возбуждения подведены к контактным кольцам 12, напрессованным на вал 1.
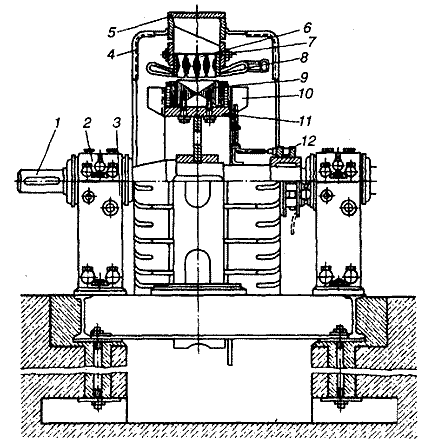 Рис. 3.41. Синхронный генератор: 1 вал; 2, 3 – крышка и стояк подшипника, 4 – кожух, 5 – корпус, 6, 8 – сердечник и обмотка статора, 7 – шпилька, 9 – полюс, 10 – вентиляторные лопатки, 11 – ротор, 12 – контактные кольца.
3.3.1.2 Технология монтажа электрических машин прибывающих с заводов изготовителей в собранном виде
При монтаже электрических машин руководствуются ПУЭ, СНиП и специальными инструкциями заводов-изготовителей. Одной из основных операций подготовительных работ перед началом монтажа является проверка фундаментов. Проверяют бетон, используемый для фундаментов; главные осевые размеры и высотные отметки опорных поверхностей; осевые размеры между отверстиями для анкерных болтов; глубину отверстий и размеры ниш в стенах фундаментов для затяжки болтов (рис. 3.42).
При проверке фундаментов размеры сверяют с данными машины: продольной осью вала машины, поперечными осями станин, реперами высоты. Проверку производят нивелиром и натянутыми визирными струнами стальных проволок.
Если при проверке обнаружится, что фундамент занижен по высоте, строительная организация обязана нарастить фундамент до требуемых размеров.
При заниженных фундаментах и общей массе машинного агрегата до 20 т допускается устанавливать машины на отрезках двутавровых балок высотой не более 100 мм; при этом следует применять только тонкие регулировочные прокладки.
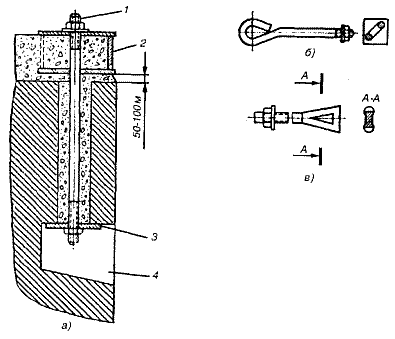 Рис. 3.42. Фундаментные болты: а – с плитками, б – крюкообразные, в – для крепления салазок; 1 – болт, 2 – плита машины, 3 – анкерная плитка, 4 – ниша.
В состав подготовительных работ входит подбор необходимых инструментов, измерительных приборов, такелажных механизмов со стропами, предварительно испытанных по правилам Госгортехнадзора. Далее производят распаковку электрических машин, очистку их от грязи, ржавчины, антикоррозионных покрытий.
Электрические машины, поступившие с завода-изготовителя в собранном виде, на месте монтажа не разбирают, если их правильно транспортировали и хранили.
Подготовка таких машин к монтажу включает в себя следующие технологические операции:
– внешний осмотр;
– очистку фундаментных плит и лап станин;
– промывку фундаментных болтов уайт спиритом и проверку качества резьбы (прогонкой гаек);
–осмотр выводов, щеточного механизма, коллекторов или контактных колец, маслоуказательной и другой арматуры;
– осмотр состояния подшипников, промывку подшипниковых стояков и картеров;
– проверку зазора между крышкой и вкладышем подшипника скольжения, валом и уплотнением подшипников, измерение зазора между вкладышем подшипника скольжения и валом;
– вскрытие подшипников качения и проверку заполнения их консистентной смазкой;
– проверку воздушного зазора между активной сталью ротора и статором;
– проверку свободного вращения ротора и отсутствие задеваний вентиляторов за крышки торцовых щитов;
– проверку мегаомметром сопротивления изоляции всех обмоток, щеточной траверсы и изолированных подшипников.
Если нет уверенности, что во время транспортировки и хранения поступившая в собранном виде машина осталась неповрежденной и незагрязненной, необходимость ее разборки для ревизии определяется специальным актом.
Монтажная организация выполняет такую работу по отдельному заказу. Сначала машины полностью или частично разбирают, а затем приступают к их осмотру. Разборку машин, поступивших в собранном виде, и последующую сборку выполняют в соответствии с инструкцией.
Монтаж электрических машин мощностью до 1000 кВт начинают с выгрузки их с транспортных средств кранами. Перемещение в горизонтальной плоскости и установку на фундамент электродвигателя выполняют с помощью электротали, электрокара или по грузчика.
Осмотр электрической машины проводят на стенде в специально выделенном в цехе помещении.
О выявленных дефектах электромонтажник ставит в известность бригадира, мастера или руководителя монтажа.
Если наружных повреждений не обнаружено, электродвигатель продувают сжатым воздухом. При этом сначала проверяют подачу по трубопроводу сухого воздуха, для чего струю направляют на какую-нибудь поверхность или на ладонь руки. При продувке ротор электродвигателя проворачивают вручную, проверяя свободное вращение вала в подшипниках. Снаружи электродвигатель обтирают тряпкой, смоченной в керосине.
Промывку подшипников скольжения во время монтажа производят следующим образом. Из подшипников удаляют остатки масла, отвернув спускные пробки. Затем, завинтив их, в подшипники наливают керосин и вращают руками якорь или ротор. Далее вывинчивают спускные пробки и дают стечь всему керосину. После промывки подшипников керосином их необходимо промыть маслом, которое уносит с собой остатки керосина. Только после этого их заполняют свежим маслом на 1/2 или 1/3 объема ванны.
Смазку в подшипниках качения (роликовых и шариковых) при монтаже машин не заменяют. Заполнение смазкой подшипника не должно превышать 2/3 свободного объема подшипника.
Измерение сопротивления изоляции электродвигателей трехфазного тока с короткозамкнутым ротором производят только обмоток статора по отношению к земле (корпусу) и друг к другу. Это возможно при выведенных шести концах обмотки. Если выведено только три конца обмотки, измерение производят только по отношению к земле (корпусу).
У электродвигателей с фазным ротором кроме определения сопротивления изоляции обмоток статора по отношению к земле и друг к другу измеряют сопротивление изоляции между ротором и статором, а также сопротивление изоляции щеток по отношению к корпусу (между кольцами и щетками должны быть проложены изолирующие прокладки).
Изоляцию обмоток электрических машин измеряют мегаомметром на 1 кВ для машин напряжением до 1 кВ и на 2,5 кВ – для машин напряжением выше 1 кВ. Если результаты измерения сопротивления изоляции обмоток электрических машин до 1 кВ удовлетворяют нормативным показателям, электрические машины могут быть включены без сушки изоляции обмоток.
Такие электродвигатели доставляют к месту монтажа, устанавливают непосредственно на полу, на специальных конструкциях, или на фундаменте. Подъем электродвигателей массой до 50 кг можно осуществлять вручную, при установке их на низкие фундаменты.
Соединение электродвигателя с приводимым им во вращение механизмом выполняют с помощью муфт или через ту или иную передачу (зубчатую, ременную). При всех способах соединения требуется проверка положения двигателя уровнем в горизонтальной плоскости в двух взаимно перпендикулярных направлениях. Для этого удобнее всего пользоваться «валовым» уровнем, т.е. таким, который в основании имеет выемку в виде «ласточкина хвоста»; его удобно накладывать непосредственно на вал электродвигателя.
Электродвигатели, устанавливаемые непосредственно на бетонном полу или фундаменте, выверяют, подкладывая под лапы электродвигателей металлические подкладки (клинья) для регулирования положения их в горизонтальной плоскости. Деревянные подкладки для этой цели не пригодны, так как при заливке фундаментных болтов цементным раствором они набухают и сбивают произведенную выверку, а при затяжке болтов спрессовываются.
При ременной и клиноременной передачах необходимо соблюдать параллельность валов электродвигателя и вращаемого им механизма, а также совпадение средних линий по ширине шкивов. Если ширина шкивов одинакова, а расстояние между центрами валов не превышает 1,5 м, выверку производят стальной выверочной линейкой (рис. 3.43, а). Для этого линейку прикладывают к торцам шкивов и подгоняют электродвигатель так, чтобы линейка касалась двух шкивов в четырех точках. Если расстояния между центрами валов более 1,5 м, а выверочная линейка отсутствует, выверку электродвигателя производят с помощью струны и временно устанавливаемых на шкивы скоб (рис. 3.43, б). Центры валов подгоняют до получения одинакового расстояния от скоб до струны. Выверку можно производить также тонким шнурком, натягиваемым от одного шкива к другому.
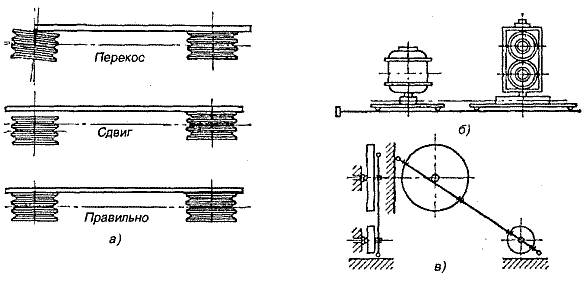 Рис. 3.43. Способы выверки установки электродвигателя при ременной и клино-ременной передачах и одинаковой ширине шкивов с помощью линейки (а), скоб и струны (б), шнурка (в).
При ременной и клиноременной передачах на вал электродвигателя часто приходится насаживать шкив, а также снимать его. Снятие шкива производят специальными скобами. Наиболее удобными являются универсальные съемники. Съемник с регулируемым раскрытием тяг производит захват детали с наружной или внутренней стороны и развивает тяговое усилие до 20 кН, съемник с самоустанавливающимися тягами от 30 кН, с гидравлическим приводом до 100 кН. Если шкив, полумуфту или шестерню не удается снять с вала, их подогревают до 250–300°С пламенем газовой горелки. При этом вал охлаждают водой или сжатым воздухом.
Для снятия подшипников качения, как правило, применяют простые съемники. Снятие производят вращением рукоятки центрального винта, упирающегося концом в торец вала. Если подшипник снять не удается, его подогревают до 100°С, поливая горячим минеральным маслом.
Новый подшипник перед посадкой на вал тщательно промывают бензином. Место посадки на валу тщательно очищают, промывают бензином и смазывают минеральным маслом. Подшипник перед посадкой прогревают в чистом минеральном масле темпера турой 80–100°С. Посадку производят отрезком трубы (желательно медной), упираемой во внутреннее кольцо подшипника. Шкив, полумуфту, шестерню насаживают на вал специальным винтовым приспособлением (рис. 3.44, а –г).
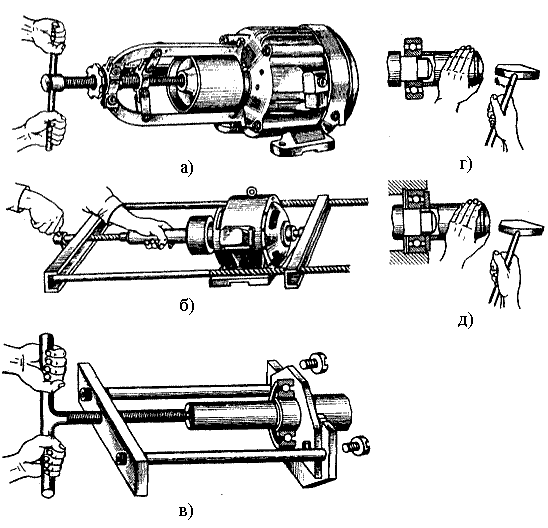 Рис. 3.44. Приемы и способы разборки электродвигателей: а – снятие шкивов и полумуфт с помощью универсального съемника с регулируемым раскрытием тяг, б – насадка шкивов и полумуфт с помощью нажимного устройства, в – снятие и насадка подшипников с помощью специального съемника, г – посадка на вал, д – посадка одновременно на вал и расточку подшипникового щита
Применение этого приспособления позволяет все горизонтальные усилия передавать на вал, а не на подшипники. Сначала снимают крышку подшипника с противоположной от привода стороны и конец вала упирают в шкворень приспособления, а затем вращением рукоятки центрального винта надвигают шкив на вал. Для насадки шкивов, полумуфт, шестерен на более крупные машины применяют винтовой домкрат, в который упирают конец вала, противоположный приводу.
Насадку шкива, полумуфты или шестерни на вал электродвигателя производят после смывания керосином с вала грязи и ржавчины. После очистки вала в канавку (выемку в валу) закладывают шпонку, конец вала слегка смазывают минеральным маслом и только после этого производят насадку.
Центровку валов соединяемых между собой машин и механизмов выполняют для устранения их боковых или угловых смещений.
В монтажной практике чаще всего используют для этого радиально-осевые скобы. Перед началом центровки полумуфты разъединяют, а валы раздвигают, чтобы скобы и полумуфты при вращении валов не соприкасались.
Конструкции радиально-осевых скоб и их крепление на ступицах полумуфт показаны на рис. 3.45. Наружную скобу 6 закрепляют хомутом 5 на ступице полумуфты 3 установленной машины, а внутреннюю скобу 1 – таким же хомутом на ступице полумуфты 2 соединяемой машины. Соединение хомутов со скобами производят болтами 4 с гайками. С помощью измерительных болтов устанавливают минимальные зазоры a и b. В процессе центровки измеряют боковые а, и угловые b зазоры, используя щупы, индикаторы или микрометры. Индикатор или микрометрическую головку ставят на место болтов 7.
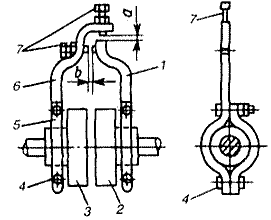 Рис. 3.45. Центровка валов с помощью радиально-осевых скоб: 1, 6 – внутренняя и наружная скобы, 2, 3 – полумуфты, 4, 7 – болты, 5 – хомут.
При измерении щупом его пластинки вводят в зазор с ощутимым трением на глубину до 20 мм. Поскольку при замерах щупом возможны погрешности, значения которых зависят от опыта проверяющего, результаты измерений необходимо контролировать, для чего проворот валов и замеры повторяют.
При правильном выполнении измерений сумма числовых значений четных замеров равняется сумме числовых значений нечетных:
и 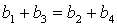
Считают, что замеры выполнены правильно, если разница между этими суммами не превышает 0,03–0,04 мм. В противном случае, не изменяя положения полумуфт, измерения повторяют более тщательно.
При центровке валов по полумуфтам (рис. 3.46) сначала крепят скобу 2 на ободе полумуфты 1 болтом. Затем определяют боковые зазоры а между измерительным болтом 4, ввернутым в скобу 2, и внешней поверхностью полумуфты. Далее замеряют угловые зазоры b при четырех положениях (0, 90, 180 и 270°) полумуфт.
Действительное значение углового зазора в каждом из четырех положений определяют как среднее арифметическое от деления суммы числовых значений b на количество замеров.
Затяжку гаек фундаментных болтов производят в два приема. При центровке валов выполняют предварительную затяжку стандартными гаечными ключами без надставок. Через 30 мин после окончания подливки бетонной смесью повторно контролируют выверенное положение электрических машин. При достижении подливкой прочности не менее 12000 кПа, но не ранее чем через 4 суток, с помощью надставок окончательно затягивают гайки фундаментных болтов.
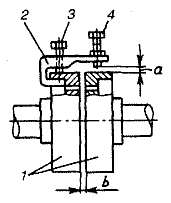 Рис. 3.46. Центровка валов по полумуфтам: 1 – полумуфты, 2 – скоба, 3, 4 – болты.
Затяжку производят равномерно в два-три обхода в требуемой последовательности. Начинают с фундаментных болтов, расположенных на осях симметрии опорной части, после чего затягивают ближайшие к ним болты, а затем, постепенно удаляясь от оси симметрии, остальные.
Крутящий момент, прилагаемый при затяжке фундаментных болтов, зависит от их диаметра. Зависимость крутящего момента от диаметра резьбы фундаментного болта приведена ниже.
Для ручной затяжки гаек фундаментных болтов применяют одно- и двусторонние гаечные ключи с открытым зевом или накидные на соответствующие размеры гаек, а также динамометрические ключи с предельным крутящим моментом до 1200 Н·м или трещоточные с моментом до 1400 Н·м, для механизированной затяжки – электро- или пневмо-гайковерты с регулируемым предельным крутящим моментом.
Диаметр резьбы фундаментного болта, мм |
16 |
20 |
24 |
30 |
36 |
42 |
Крутящий момент, Н·м |
30 – 60 |
50 – 100 |
130 – 50 |
300 – 550 |
600 – 950 |
1000 – 1500 |
3.3.1.3 Технология монтажа электрических машин прибывающих с заводов изготовителей в разобранном виде
Перед началом монтажа машин по акту производят приемку фундаментов от строительной организации. Очищают резьбовые отверстия фундаментных плит, проверяют качество резьбы и при необходимости исправляют ее. В отверстия фундамента закладывают фундаментные болты, а по периметру фундаментной плиты укладывают стальные или чугунные подкладки. Плиты, имеющие нижние полки, устанавливают на подкладки и клинья, которые размещают в местах сосредоточенных нагрузок.
Плиты, не имеющие нижних полок, устанавливают на подкладки и клинья, укладываемые под ребра жесткости, расположенные в непосредственной близости от фундаментных болтов, под подшипниковые стояки, лапы станин и остальные ребра так, чтобы расстояние между осями соседних подкладок было не более 1 м. Подкладки из-под плиты должны выступать на 35–50 мм. Подготовленную к монтажу плиту устанавливают краном на подкладки, уложенные на фундамент. Плиту ориентируют по осям фундамента визирными струнами (рис. 3.47). Далее фундаментную плиту выверяют по уровню, добиваясь горизонтальности тонкими стальными подкладками. Подкладки размещают под плиту, приподнимая ее клиновыми или гидравлическими домкратами. При выверке плиты применяют длинную линейку и обычный или гидростатический уровень. После выверки плиты производят ее крепление затяжкой фундаментных болтов.
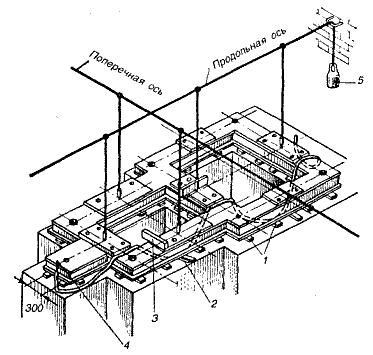 Рис. 3.47. Разметка осей и установка фундаментной плиты электрических машин большой мощности: 1 – подкладки, 2 – стальной клин, 3 – строительный уровень, 4 – гидростатический уровень, 5 – груз.
Если при сооружении фундамента анкерные болты не были установлены, электрическую машину устанавливают на приклеенных анкерных болтах, размещаемых в пробуренных в фундаменте колодцах (рис. 3.48).
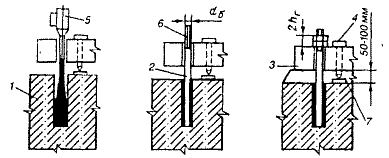 Рис. 3.48. Установка анкерных болтов на эпоксидном клее для крепления электрических машин: 1 – фундамент, 2 – штанга перфоратора с коронкой, 3 – опорная плита машины, 4 – отжимной болт, 5 – воронка для заливки эпоксидным клеем, 6 – анкерный болт, 7 – бетонная подливка.
При бесподкладочном способе монтажа зазор между поверхностью бетонного фундамента и основанием плиты оставляют 50 – 60 мм. Площадку под установку домкратов выверяют в горизонтальной плоскости по уровню. Домкраты устанавливают у фундаментных болтов и в местах сосредоточенных нагрузок. Суммарная грузоподъемность домкратов должна быть не менее 1,5-кратной монтажной массы оборудования. После окончательной выверки плиты, установленной на домкратах, производят подливку плиты, за исключением мест установки домкратов, которые выгораживают временной опалубкой. Подливку вибрационным способом производит строительная организация, наблюдение за тщательностью подливки ведут ответственные представители электромонтажной организации. После затвердевания подливки снимают домкраты и производят окончательную подливку фундаментной плиты в этих местах. Подливку принимают по акту, в котором должны быть указаны: состав бетонной смеси, количество пластифицирующих добавок,
температура бетонной смеси и воздуха во время подливки и вибрирования.
Далее затягивают фундаментную плиту и устанавливают подшипниковые стойки, предварительно прошедшие ревизию. Под подшипниковые стойки помещают металлические (регулировочные) и в необходимых случаях изоляционные прокладки.
Сопротивление, изоляции подшипниковых стоек по отношению к плите должно составлять не менее 0,5 МОм; при этом болты крепления стойки к плите должны быть затянуты до укладки валов в подшипники.
После установки вала ротора в подшипники специальным инструментом – шабером, которым удаляют выступающие неровности с поверхности баббитового вкладыша подшипника, подгоняют рабочую поверхность подшипникового вкладыша к шейке вала.
Для заводки ротора массой до 5 – 6 т в неразъемные статоры применяют приспособление, состоящее из направляющей детали, укрепляемой на корпусе статора, и кареток на шарикоподшипниках, снабженных устройствами для подвески и перемещения ротора (рис. 3.49).
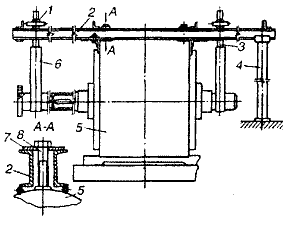 Рис. 3.49. Приспособление для выкатки и заводки роторов массой до 5 т: 1 – каретка, 2 – направляющие швеллеры, 3 – натяжно-подьемный болт, 4 – подпорная стойка, 5 – статор, 6 – подъемная лента, 7 – накладка, 8 – болт.
Ответственной операцией монтажа является центровка валов. Несоосность валов характеризуется относительным смещением их осей в радиальном и угловом направлениях. В крупных машинах валы имеют естественный прогиб, поэтому трудно добиться строгой параллельности торцовых плоскостей соединительных полумуфт.
При центровке валов допускают отклонения в радиальном и угловом направлениях в пределах 0,03 – 0,6 мм в зависимости от конструкции соединительной муфты.
Выверку и регулировку воздушного зазора выполняют после окончательной центровки валов, а у машин постоянного тока с разъемным статором – после установки его верхней половины и скрепления последней болтами с нижней половиной. Для этого используют специальные и клиновые щупы (рис. 3.50, а, б). Воздушный зазор измеряют с обеих сторон ротора или якоря в следующих местах: у машин с неявно выраженными полюсами – в четырех точках (при большом диаметре ротора – в восьми); у машин с явно выраженными полюсами – под каждым полюсом против середины полюсного башмака.
Допустимая разность между наибольшим и наименьшим значениями воздушных зазоров в процентах от среднеарифметического не должна превышать у машин: асинхронных и синхронных тихоходных – 10%, быстроходных – 5%, постоянного тока с петлевой обмоткой – 10% (при зазоре до 3 мм) и 5% (при зазоре более 3 мм), с волновой обмоткой эту разность увеличивают в 2 – 2,5 раза. Зазоры между якорем и добавочным полюсом не должны отличаться более чем на 5%. Неравномерность воздушного зазора для всех электрических машин не должна превышать 10%.
Воздушный зазор регулируют подбором соответствующих подкладок под лапы станины статора и его разворотом в поперечном Направлении относительно продольной оси ротора или якоря.
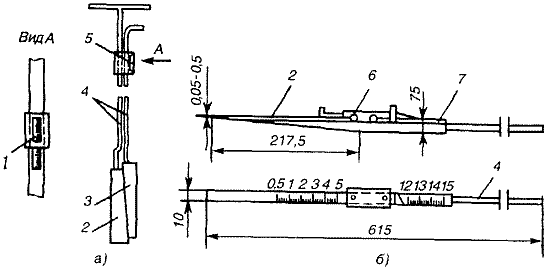 Рис. 3.50. Щупы: д – специальный, б – клиновой; 1 – нониус, 2, 3–клинья, 4 – стержни, 5 – обойма, 6 – движок, 7 – указатель.
Сушку обмоток машины производят в том случае, если при ревизии установлен низкий уровень изоляции, не допускающий включения без сушки.
Сушка обмоток может быть выполнена их нагревом: постоянным или переменным током от постороннего источника; горячим воздухом (обдув); потерями в стали (индукционным способом); током КЗ при пониженном напряжении (для генераторов); инфракрасным облучением (радиационный способ).
Перед сушкой обмотки продувают чистым и сухим воздухом для того, чтобы осевшая пыль после разогрева и размягчения изоляции не прилипала к ее лаковой покровной пленке.
В процессе сушки термометром или термопарой непрерывно измеряют температуру обмоток и стали, не допуская повышения ее выше 75 °С. Температуру нагрева увеличивают постепенно – быстрый нагрев может вызвать разрывы в изоляции: при сушке крупных машин температуру увеличивают до 50°С в течение 20 ч; наивысшая температура должна быть достигнута не ранее чем через 30 – 40 ч.
Сушку обмоток считают законченной, если при установившейся температуре сопротивление изоляции и коэффициент абсорбции обмоток не изменяются в течение 6 – 7 ч.
Технологическая последовательность монтажных работ при установке машин большой мощности заключается в распаковке и размещении частей машины на монтажной площадке в машинном зале; очистке частей машины от грязи и ржавчины, очистке поверхности фундамента, выверке в горизонтальной плоскости основания фундаментной плиты; установке подшипниковых стояков и изоляции от фундаментной плиты тех из них, для которых она предусмотрена предприятием-изготовителем; установке статора и ротора; сопряжении валов; подгонке подшипников и вкладышей, уплотнении подшипников; выполнении внутренних соединений машины; обработке коллектора и контактных колец; монтаже коммутирующих устройств (суппорт, траверсы, щетки); проверке со стояния изоляции и при необходимости контрольном прогреве или сушке; установке контрольных шпилек (конических штифтов) для надежного фиксирования положения станин и подшипниковых стояков; монтаже систем смазки и принудительной вентиляции.
Набор инструмента для монтажа электрических машин, поступающих в собранном или разобранном виде, следующий: приспособление для развертывания отверстий в полумуфтах и проворачивания валов, съемник подшипников качения со скобой и хомутом, гидравлический домкрат до 100 кН, приспособление для центровки валов, клиновой щуп для измерения воздушных зазоров, ключ со сменными головками для гаек большого размера, приспособление для центровки машин с промежуточными валами, виброметр, трехзахватный универсальный съемник, клиновой домкрат грузоподъемностью 50 кН, элёктрошарошка, гидростатический уровень, разъемный регулируемый уровень, микрометрический уровень с ценой деления 0,1/1000 мм, набор инструмента слесаря-монтажника, центробежный ручной тахометр ИО-10, комплекты конических разверток 1:50 диаметром 13 – 27 мм, микрометрических нутромеров для измерения в пределах 50 – 600 мм, индикаторных скоб С – 300 – 800 мм, гаечных ключей размером 8 – 36 мм,
комплекты щупов, отвесов и стропов, призма длиной 100 – 150 мм.
3.3.1.4. Технология монтажа взрывозащищенных электродвигателей
Как правило, взрывозащищенные электродвигатели поступают с заводов-изготовителей в собранном виде, вместе с технологическим оборудованием. Каждый электродвигатель поставляют с техническим паспортом и инструкцией по монтажу и эксплуатации.
Разборку электродвигателей при монтаже проводят в том случае, если обнаружен обрыв обмоток, или недопустимое снижение сопротивления изоляции по отношению к корпусу.
Для электродвигателей на напряжение 6 или 10 кВ сопротивление изоляции обмоток измеряют мегаомметром на 2500 В, при этом оно должно быть не ниже 6 МОм.
Если сопротивление изоляции обмоток электродвигателя ниже нормы, осуществляют сушку обмоток со снятием вводного устройства для циркуляции воздуха независимо от срока отгрузки с завода-изготовителя.
После сушки проверяют плотность прилегания сопрягаемых деталей взрывонепроницаемых оболочек. Зазор должен быть не больше указанного в заводской инструкции по монтажу и эксплуатации электродвигателя. Если электродвигатель не удовлетворяет этим требованиям, его нельзя использовать как взрывозащищенный.
Электродвигатели серии ВАО на напряжение 380/660 В мощностью до 315 кВт имеют шесть типов вводных устройств К1–К6, которые допускают непосредственный ввод бронированных кабелей с бумажной изоляцией, кабелей и проводов в трубах с изоляцией жил из резины и поливинилхлоридного пластиката.
Устройства К5 и К6 электродвигателей ВАО 315–450 имеют отверстия для ввода двух кабелей и отличаются друг от друга только диаметрами вводных отверстий. Вводные устройства крепят к фланцам электродвигателей четырьмя болтами и могут быть повернуты на 90°, т.е. установлены вводными отверстиями влево, вправо, вверх и вниз.
Внутри корпусов вводных устройств электродвигателей 0–9-го габаритов установлено по три силовых проходных контактных зажима и один заземляющий зажим у электродвигателей 315–450-го габаритов – шесть силовых и два заземляющих зажима (рис. 3.51). Силовые зажимы соединены попарно контактными пластинами с отверстиями диаметром 10 мм, что позволяет присоединять к одной фазе по одной жиле каждого из двух вводимых кабелей. При этом контактные плоскости наконечников фазных жил одного кабеля должны быть повернуты на 180° по отношению к контактным плоскостям наконечников другого кабеля для присоединения наконечников одной фазы с двух сторон контактной пластины.
При вводе одного кабеля в электродвигатели серии ВАО 315 – 450 категорически запрещается снимать из второго вводного отверстия заводскую заглушку во избежание нарушения взрывозащищенных свойств вводного устройства. Вводные устройства электродвигателей серии ВАО маркировки В4Г и В4Д с 0-го по 9-й габариты – стальные сварные, расположены сверху электродвигателей и могут быть повернуты на 90°. Для электродвигателей 0–5-го габаритов используют вводное устройство типа К1, 6–9-го габаритов – К3.
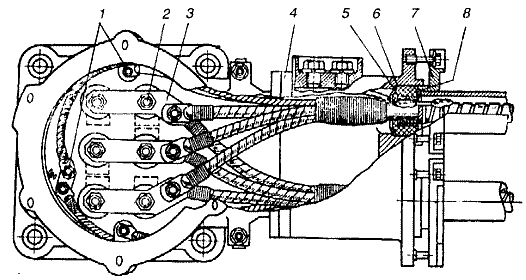 Рис. 3.51. Смонтированное вводное устройство электродвигателей ВАО 315-450-го габаритов: 1 – заземляющий зажим, 2 – силовой зажим, 3 – контактная пластина, 4, 6 – кабельная и нажимная муфты, 5 – уплотнительное кольцо, 7, 8 – упорная и нажимная шайбы.
Перед вводом проводов и кабелей в электродвигатели сначала с корпуса вводного устройства снимают нажимную муфту, затем из гнезда кабельной муфты вынимают нажимную шайбу и удаляют надрезанные слои резинового кольца или сверлят в кольце отверстие по диаметру оболочки кабеля. Диаметр отверстия не должен превышать диаметра оболочки кабеля более чем на 1 – 1,5 мм (кольцо надевают на наружную оболочку кабелей марок ВБВ и АВБВ).
При вводе проводов в резиновое кольцо по меткам сверлят четыре отверстия диаметром, равным диаметру вводимого провода, и снимают крышку, отвернув торцовым ключом болты, крепящие ее к корпусу вводного устройства. При подводе к электродвигателям кабелей марок ВБВ и АВБВ от основной трассы их прокладывают открыто на перфорированных лотках или монтажных профилях без дополнительной зашиты от возможных механических воздействий и независимо от высоты прокладки. Если расстояние от нижней муфты вводного устройства электродвигателя до места крепления кабеля на лотке не более 0,7 м, дополнительных креплений кабеля не делают, а при больших расстояниях ставят перфорированный лоток с прокладкой по нему кабеля. Варианты подвода кабелей марок ВБВ и АВБВ к электродвигателям приведены на рис, 3.52.
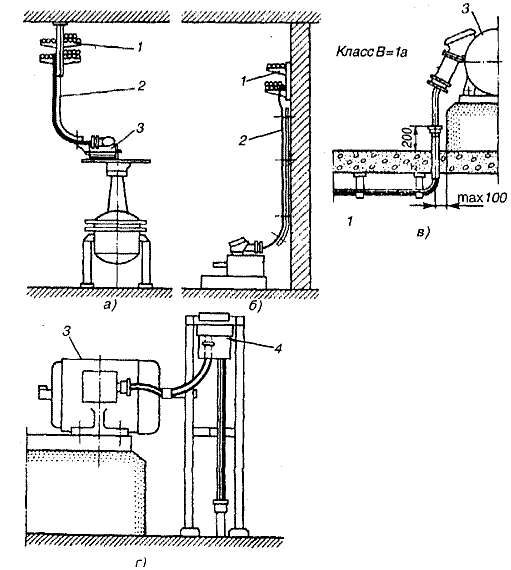 Рис. 3.52. Варианты подвода к электродвигателям кабелей марок ВБВ и АВБВ: а – сверху, б – по стене сверху, в – снизу сквозь перекрытия, г – через пускатель; 1 – кабельная конструкция, 2 – лоток, 3 – электродвигатель, 4 – пускатель.
Открыто прокладываемые бронированные и небронированные кабели других марок с поливинилхлоридной, резиновой и бумажной изоляцией (например: ВВБГ; ВРБГ; СБГ и др.), при подводе к электродвигателям защищают от возможных механических воздействий на высоте не ниже 2 м от пола или площадки обслуживания. Защиту кабеля осуществляют монтажными профилями, стальными коробами, водогазопроводными трубами.
При подводе к электродвигателям проводов или кабелей в трубах, выходящих из пола, трубы должны иметь привязку, указанную в проекте. После установки электродвигателей на место трубы доводят до вводного устройства и вводят на короткой резьбе в нажимную муфту. Защиту бронированных кабелей на участке между трубами, выходящими из пола, и вводным устройством электродвигателя можно выполнять монтажным профилем или стальным коробом.
При замере трубы нажимную муфту притягивают болтами до отказа к кабельной муфте (или корпусу вводного устройства у электродвигателей до 3-го габарита). Болты затягивают равномерно во избежание перекоса нажимной муфты и повреждения резьбы болтов.
Если диаметр подводимой трубы меньше диаметра отверстия в нажимной муфте вводного устройства, в нажимную муфту ввертывают переходную футорку. При выводе труб из пола они имеют разъемные соединения. Если кабель затянут в трубу до установки электродвигателя, разъемное соединение не собирают.
К электродвигателям, которые установлены на основаниях, подверженных вибрации, подвод выполняют так:
– во взрывоопасных зонах всех классов – гибкими переносными кабелями с резиновой изоляцией (от пусковых аппаратов, установленных как у электродвигателей, так и в электропомещениях (без дополнительной защиты от механических повреждений);
– во взрывоопасных зонах классов В-16, В-1г – гибкими проводами в водогазопроводных трубах с переходом на резиновые напорные рукава при условии их соответствия окружающей среде (пары бензина, бензола и т.п.);
– во взрывоопасных зонах классов B-la, B-1 – гибкими проводами в водогазопроводных трубах с переходом на герметичные металлорукава типа PI-Ц-А и РП-Ц-А.
Для соединения герметичных металлорукавов с электродвигателями и аппаратами в отверстие вводного устройства ввинчивают штуцеры или к трубе привинчивают накидную гайку металлорукава.
3.3.2. Технология монтажа средств автоматизации
К средствам автоматизации, относятся устройства позволяющие автоматизировать какой либо технологический процесс, то есть управлять им без участия человека.
Простейшими устройствами являются выключатели [47, 48] (концевые – рис. 3.53, путевые и др.) при помощи которых можно организовать автоматическое отключение (включение, переключение) процессов связанных с движением или перемещением. Конструкция данных выключателей представляет собой закрытый подвижный контакт (контакты) механически соединенный с рычагом или тягой, при воздействии на который контакт замыкается или размыкается. Данные контакты включаются в цепи управления магнитных пускателей отвечающих за включение и выключение электродвигателей. Примерами использования концевых и путевых выключателей являются лифт и навозоуборочный транспортер (с работой навозоуборочного транспортера можно познакомиться в лабораторной работе № 11), перемещение которых автоматически прекращается при достижении определенного положения и нажатии на рычаг такого выключателя.
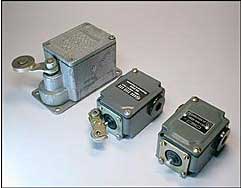 Рис. 3.53 Концевые и путевые выключатели с различными типами нажимных устройств, слева направо – поворотного типа с роликом, нажимного типа с роликом, нажимного типа.
Более сложными средствами автоматизации являются реле (промежуточные, времени – рис. 3.54, тока, напряжения) и датчики (влажности, температуры, уровня, и др.). С помощью датчиков контролируются необходимые значения параметров. Конструкция простейших датчиков представляет собой механизм чувствительный к контролируемому параметру и один или несколько подвижных контактов механически соединенных с чувствительным элементом. Данные контакты включаются в цепи управления магнитных пускателей отвечающих за включение и выключение электродвигателей. В случае, когда используемые контакты слабые и не рассчитаны на протекание необходимого тока, тогда используют промежуточные реле, в цепь управления (катушки) включается контакт датчика, при замыкании которого срабатывает промежуточное реле и замыкает или размыкает свои контакты, уже через которые осуществляется управление технологическим процессом.
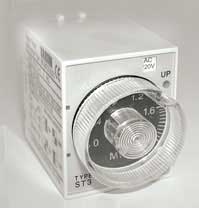 Рис. 3.54. Общий вид реле времени SASSIN.
С помощью реле времени можно задавать промежутки времени на включение или отключение технологического оборудования в цепь управления которого установлены контакты данного реле. В настоящее время существует большой выбор как механических так и электронных реле времени которые позволяют программировать управление технологическим процессом в течение суток или даже недели.
Реле тока и напряжения способны реагировать на величину контролируемого параметра (тока или напряжения) и срабатывать в зависимости от этой величины. Данные реле могут использоваться как непосредственно для контроля данных параметров (в силовых сетях технологического оборудования), так и для контроля косвенных параметров. Например: в системе контроля температуры, с датчиком температуры, основанным на нелинейном сопротивлении, при увеличении температуры сопротивление падает, увеличивается ток в контролируемой цепи, срабатывает реле тока и отключает нагревательную установку.
Еще более сложными средствами автоматизации являются устройства, основанные на датчиках и микропроцессорных контролерах. Данные устройства позволяют осуществлять регулирование и контроль параметров в широком диапазоне. Как правило, данные устройства разрабатываются крупными научно исследовательскими и производственными предприятиями и выпускаются комплектно для контроля какого либо параметра.
Данные датчики, как правило, изготавливают из материалов имеющих нелинейные характеристики. Например: нелинейное сопротивление материала в зависимости от температуры окружающей среды, при изменении температуры изменяется сопротивление элемента, соответственно ток, протекающий через него при приложенном постоянном напряжении, будет изменяться. Теперь, зная характеристику зависимости сопротивления от температуры, можно по величине протекаемого тока определить температуру окружающей среды. Для контроля температуры необходим контроллер, в настоящее время широко используются микропроцессорные контролеры, который бы контролировал величину прикладываемого напряжения и величину протекаемого тока, вычислял значение температуры и подавал управляющий сигнал на управляемое устройство.
Более подробно различные датчики, регуляторы и схемы управления вами будут рассмотрены при изучении дисциплины "Автоматика".
|