Электровзрывная обработка
6.1 Схемы выпрямителей для электровзрывной обработки
6.2 Физические процессы при электроимпульсном разрушении материалов
6.3 Бурение скважин
6.4 Разрушение бетона и железобетона
6.5 Дробление руд
6.6 Штамповка, выдавливание и вытяжка деталей
6.7 Раздача труб
6.8 Электроимпульсное дробление глубокоохлажденных резин и резинотех
Магнитно-импульсные технологии
6.9 Физические основы магнитно-импульсных технологии
6.10 Технологические операции, выполняемые магнитно-импульсным способом
Электроэрозийная обработка материалов
6.11Физические основы электроэрозийной обработки
6.12 Технологические процессы изготовления деталей и показатели ЭЭО
6.13 Системы очистки и подачи рабочей жидкости
Контрольные вопросы
Электровзрывная обработка
6.1 Схемы выпрямителей для электровзрывной обработки
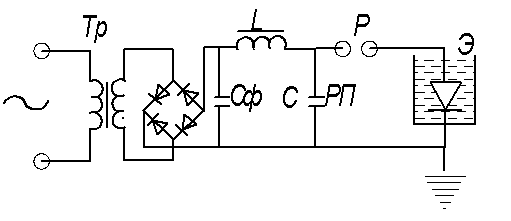 |
4 6.1. Схема выпрямителя на постоянном токе. |
Принцип работы выпрямителей, применяемых в электровзрывных технологиях заключается в заряде конденсатора высокого напряжения до необходимой величины и его разряде через разрядный промежуток и последовательно соединенный с ним формирующий промежуток (разрядник). Роль формирующего промежутка заключается в формировании импульса необходимых параметров - повышение крутизны фронтов и сокращение длительности.
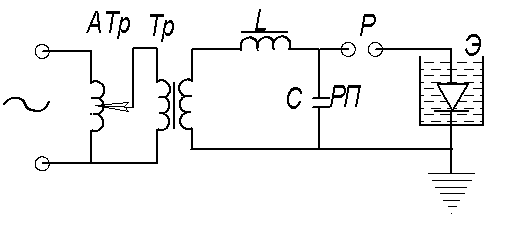 |
Рис. 6.2. Схема выпрямителя на переменном токе |
Разработано большое число выпрямителей, различающихся наличием дополнительных элементов: автотрансформатора, ограничивающего сопротивление и емкость в первичной цепи, фильтра, состоящего из конденсатора и индуктивности (дросселя). На рис. 6.1 и 6.2 приведены схемы выпрямителей на переменном и постоянном токе.
Здесь АТр - автотрансформатор, L - дроссель, Сф - конденсатор фильтра.
6.2 Физические процессы при электроимпульсном разрушении материалов
При разрушении материалов электроимпульсным способом используется зависимость прочности диэлектрической среды от длительности импульса. С уменьшением времени воздействие импульсного напряжения прочность жидких диэлектриков растет быстрее, чем твердых диэлектриков. Если при статическом напряжении (Uст) электрическая прочность твердых диэлектриков, как правило, превышает прочность жидких диэлектриков, то при импульсном напряжении (Uимп) при длительности импульса менее 10-1с электрическая прочность жидких диэлектриков возрастает так, что становится выше прочности твердых диэлектриков и горных пород.
При помещении материалов в жидкость, например в техническую воду, и при подаче на приложенные к материалу электроды импульса напряжения с очень крутым передним фронтом произойдет электрический пробой по объему твердого тела между электродами и дальнейшее его разрушение.
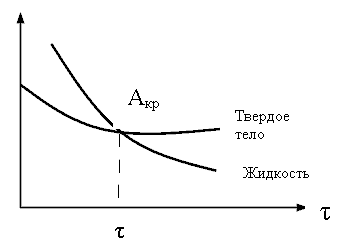 |
Рис. 6.3. |
На рис. 6.3 показаны Вольт-секундные характеристики (зависимость пробивного напряжения Uпр от длительности импульса) твердого тела и жидкости. Из рисунка следует, что до критической точки (Акр) при длинных импульсах пробивное напряжение у твердого тела выше, чем у жидкости.
При меньших значениях Uпр ситуация противоположная - электрическая прочность жидкости выше электрической прочности твердого тела. Поэтому при осуществлении технологических операций разрушения материалов длительность импульса должна быть меньше значения τкр для данной жидкости и твердого тела.
При разрушении различных материалов необходимо подбирать соответствующую жидкость. В реальных установках, как правило, используется вода, трансформаторное масло, дизельное топливо.
Электроимпульсный способ используют для бурения скважин, дробления материалов, разрушения железобетонных изделий. На рис. 6.4 показаны принципиальные схемы бурения скважин и разрушения железобетонных изделий электроимпульсным способом.
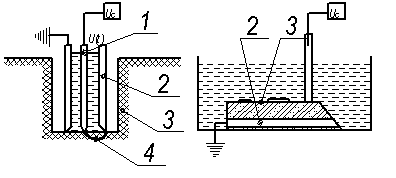 |
Рис.6.4 |
Принципиальная схема бурения скважин (а) и разрушения железобетонных изделий (б) электроимпульсным способом. 1-высоковольтный электрод, 2-заземленный электрод, 3- разрущаемая порода, 4- искровой канал, UC;-источник высокого напряжения
6.3 Бурение скважин
Бурение скважин электроимпульсным способом эффективно для прочных и особо прочных пород и для мерзлых грунтов. Диаметр скважины должен быть не менее 100-150 мм, так как эффективность бурения увеличивается с увеличением диаметра. Эффективность по сравнению с механическим способом бурения возрастает для скважин некруглого сечения, при бурении в затрудненных для вращения условиях (под водой, в условиях ограниченного пространства).
6.4 Разрушение бетона и железобетона
Разрушение бетона и железобетона является важной проблемой, поскольку при их производстве значительную долю составляет некондиционная часть продукции. Кроме того, источниками отходов являются сносимые здания и сооружения, автодорожные покрытия. Переработка указанных отходов позволяет вернуть металлическую арматуру и минеральное сырье в производство и решить дополнительные проблемы (освобождение земельных угодий, очистку территорий и т. д.).
При механических способах разрушения себестоимость операций очень высокая за счет износа разрушающего инструмента, низкого КПД, трудностей концентрации достаточного количества энергии. Проблема усложняется тем, что необходимо полностью отделить бетон от арматуры.
Электроимпульсная технология является безотходной, т.к. позволяет полностью разделить бетон и арматуру, причем арматурный каркас может быть использован повторно.
6.5 Дробление руд
Дробление руд электроимпульсным способом позволяет получить фракции необходимого размера. Особенно благоприятными для данного способа являются геологические объекты и искусственные материалы, в которых электрические и физико-механические свойства полезного компонента и вмещающих руд сочетаются так, что полезный компонент обладает высокой электрической прочностью и пластичностью, а вмещающая порода обладает меньшей электрической прочностью и высокой хрупкостью.
При электрическом способе дробления таких пород, пробой осуществляется во вмещающей породе, которая, хрупко разрушаясь, измельчается, оставляя не поврежденными крупные кристаллы.
Особенность электроимпульсного способа дезинтегрировать компоненты руд по пробивному напряжению позволяет достигать высокой производительности данной технологии и реального ее применения на обогатительных фабриках.
6.6 Штамповка, выдавливание и вытяжка деталей
Данные операции позволяют получать из листов различных металлов и сплавов детали различной конфигурации и формы. Например, получать детали сферической или конической формы, получать гофры на трубчатой заготовке. В этой технологии используют давление ударной волны, образованной при подаче импульсного напряжения на электроды и возникновении разряда.
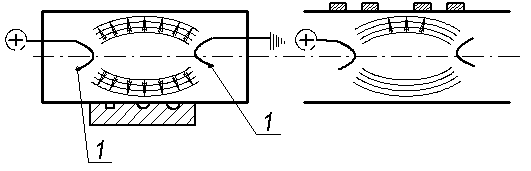 |
Рис. 6.5 |
Схемы электровзрывного получения гофр на трубчатой заготовке и штамповки плоской заготовки показаны на рис. 6.5
6.7 Раздача труб
Для получения труб такой формы, чтобы на концах они имели сужение, через которое производилась бы их стыковка, используют безматричную раздачу тепловым взрывом.
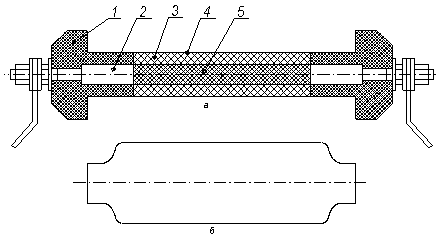 |
Рис. 6.6 |
Принцип работы такой технологии заключается в испарении помещенного внутрь трубы взрывного стержня при подаче на него импульса напряжения и образовании необходимого объема газов. Образованные при взрыве газы разогревают и раздавливают полиэтиленовую втулку, вставленную в трубу, которая в свою очередь раздавливает трубу. Если труба на концах не имеет полиэтиленовой вставки и взрывного стержня и в концы вставлены упоры, например из текстолита, то они остаются без изменения и после обработки их диаметр становится меньше диаметра всей трубы. Схема раздачи труб показана на рис. 6.6.
6.8 Электроимпульсное дробление глубокоохлажденных резин и резинотехнических изделии, армированных металлом
Постоянное накопление резиновых и полимерных отходов требует эффективных методов их переработки с целью возврата в производство ценного сырья и улучшения экологического состояния территорий. В настоящее время наиболее перспективной является переработка отходов резиновой промышленности и резинотехнических изделий, включающая их предварительное измельчение. Для этого необходимы рациональные способы получения из них резиновой крошки различной степени дисперсности. В последние 10-15 лет для этого традиционно используется техника криогенного измельчения, реализующая разрушение материала, охлажденного до температуры хрупкости, на механических установках. Такая технология имеет два существенных недостатка при переработке резино-металических отходов:
1) значительный износ рабочих инструментов;
2) большая толщина металлических включений (более 2-3 мм)
При электроимпульсном дроблении рабочим инструментом являются электрические разряды, процесс разрушения можно регулировать величиной энергии и длительностью импульса, что позволяет получать крошку заданной дисперсности. Кроме того, при разрушении резинотехнических изделий, армированных металлом, возможно полное отделение резины от металла.
В таблице 6.1 приведены значения энергии импульса (\У), производительности импульса (а), условных энергозатрат (А) при дроблении резин марки ШБТМ и ТСШ электроимпульсным методом.
Оптимальная частота посылки импульсов составляет 6-8 имп/с, расход жидкого азота для охлаждения равен 0,005 лс/имп. Сравнение абсолютных значений удельных показателей энергетических характеристик разрушения горных пород и резинотехнических изделий показывает, что для горных пород они на порядок выше.
Таблица 6.1 Значения параметров дробления резин электроимпульсным методом
Марка резины | Размеры, мм | W, Дж | А, Г/имп. | А, кВтч/кг |
исходный | конечный |
ШБТМ | 30-50 | 2 | 550 | 1,01 | 0,1 |
1 | 630 | 0,63 | 0,16 |
ТСШ | 30-50 | 2 | 580 | 1.15 | 0.1 |
1 | 700 | 0.47 | 027 |
Магнитно-импульсные технологии
6.9 Физические основы магнитно-импульсных технологии
Физика процессов в токопроводящих материалах под действием импульсного магнитного поля.
При взаимодействии импульсного электромагнитного поля с током, индуцированным этим полем в токопроводящих материалах осуществляется их деформация. Между индуцированным током и электромагнитным полем возникает взаимодействие, которое создает значительные силы давления, деформирующие токопроводящий материал-заготовку. Величина давления определяется индукцией поля.
Деформацию осуществляют двумя путями:
1) электродинамическим при взаимодействии токов в возбудителе и заготовке, включенной в цепь разряда конденсатора, создающего магнитное поле;
2) индукционным при взаимодействии импульсного магнитного поля с наведенными этим же полем в заготовке токами; при этом заготовка не включена в электрическую цепь, создающую поле.
Индукционный способ. Этот способ получил более широкое распространение, так как заготовка в этом случае не включена в электрическую цепь, что упрощает схему.
Электродинамический способ основан на законе электротехники о взаимодействии двух параллельных проводников, по которым протекает ток. Сила взаимодействия, возникающая между проводниками пропорциональна произведению силы токов, длине проводников и обратно пропорционально расстоянию между ними:
где I1, I2; - силы токов, протекающих по проводникам;
r - расстояние между ними;
l- длина проводников;
α- коэффициент пропорциональности.
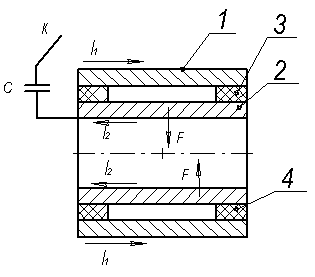 |
Рис. 6.7 Схема электродинамического способа. |
Если одним проводником сделать катушку, другим - заготовку и соединить их электрически, то при подаче импульса напряжения через конденсатор в катушке возникнет магнитное поле, которое будет действовать на заготовку с силой F. Схема электродинамического способа показана на рис. 6.7.
I1, I2 - токи в катушке (1) и заготовке (2), С - конденсатор, 3 -кольцевая перемычка, обеспечивающая электрический контакт, 4 - диэлектрическая кольцевая вставка.
Силы F, действующие на заготовку, изменяют ее профиль по любой форме матрицы, вставленной внутрь заготовки. Если изменить схему так, чтобы катушка была внутри заготовки, тогда матрицу необходимо надеть на заготовку, при этом будут действовать растягивающие заготовку силы.
При индукционном способе заготовка не является частью электрической цепи. Токи, наведенные в ней электромагнитным полем, взаимодействуют с полем. Силы взаимодействия осуществляют деформацию заготовки по форме матрицы.
Плотность магнитной энергии (ρm), действующей на заготовку определяется выражением:
где μо - магнитная постоянная, равная 4π 107, гН/м. Плотность энергии пропорциональна давлению, действующему на заготовку. Величину давления можно рассчитать по выражению:
где Р - давление, кг/см2;
Вмах - максимальное значение индукции в импульсе, Тс. Энергия магнитного поля определяется индуктивностью катушки (L) и силой тока (I) согласно выражения:
Скорость деформации заготовки зависит от величины магнитной индукции и плотности материала заготовки:
где d - плотность материала заготовки, г/см3
Толщина заготовки h должна быть больше глубины проникновения магнитного поля в материал δ, определяемой выражением:
где ρ - удельное сопротивление материала,
τ - длительность полуцикла импульса тока.
При магнитном формообразовании энергия магнитного поля расходуется на создание давления и на нагревание заготовки.
Повышение температуры поверхности заготовки на глубине проникновения магнитного поля определяется величиной поля и удельной теплоемкостью (ср) материала согласно выражения:
Нагрев заготовки оказывает сильное влияние на ее деформацию. В некоторых случаях заготовка разогревается до 1000 - 3000 К. Подбором условий обработки можно изменять соотношение между механической и тепловой составляющими воздействия и создать условия обработки заготовок из материалов, не проявляющих пластичности при нормальной температуре.
В таблице 6.2 приведены значения электрического сопротивления и глубины проникновения магнитного поля для некоторых металлов и сплавов. Из таблицы следует, что с увеличением удельного электрического сопротивления возрастает глубина проникновения магнитного поля, а с увеличением частоты она уменьшается. Для различных материалов, в зависимости от частоты, глубина проникновения изменяется от десятых долей до десятков миллиметров.
Таблица 6.2
Материал | ρ 106, Ом/м | Глубина проникновения (мм) при частоте разрядов, кГц. |
1 | 10 | 20 | 50 |
Серебро Медь Золото Алюм. сплав АДМ Латунь Л96 Бронза Бр А5 Углерод, сталь 20 Титан, сплав ВТ51 | 1.6 1.78 2.2 2.92 4.3 9.95 24.2 138 | 2.01 2.12 2.36 2.72 3.3 5.02 6.0 18.7 | 0.64 0.67 0.75 0.86 1.04 1.59 1.9 5.91 |
0.45 0.48 0.57 0.61 0.82 1.12 1.34 418 | 0.28 0.3 0.33 0.38 0.47 0.71 0.85 2.65 |
Принципиальная схема установки для магнитно-импульсной обработки.
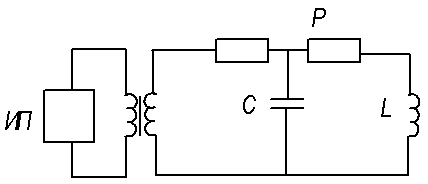 |
Рис. 6.8. Принципиальная схема установки магнитно-импульсной обработки |
Принципиальная схема установки для магнитно-импульсной обработки по казана на рис. 6.8.
Зарядка конденсатора С осуществляется источником тока ИП через трансформатор Тр и выпрямитель В. Разрядка конденсатора на индуктор L осуществляется с помощью разрядника Р. Запасенная в конденсаторе энергия определяется его емкостью и величиной напряжения:
Ток, протекающий в разрядной цепи определяется напряжением и параметрами цепи. Сила тока изменяется со временем по закону:
где L - индуктивность разрядной цепи, R - активное сопротивление разрядной цепи, ω - круговая частота тока разряда .
Амплитудное значение напряженности магнитного поля, создаваемого в индукторе зависит от электрических параметров цепи и формы индуктора и определяется выражением:
где r и l - радиус и длина индуктора соответственно; k1 -коэффициент, зависящий от формы индуктора и скорости затухания колебаний в контуре и изменяющийся от 0 до 2.
Длительность полуцикла импульса давления обратно пропорциональна частоте тока импульса и для трубчатой заготовки может быть определена выражением:
где Д - диаметр заготовки, l - величина зазора между индуктором и заготовкой с учетом глубины проникновения магнитного поля, к2 -коэффициент пропорциональности.
6.10 Технологические операции, выполняемые магнитно-импульсным способом
Особенности магнитно-импульсного формообразования.
Магнитно-импульсные технологии имеют ряд особенностей, отличающих их от других технологий.
1. Метод наиболее эффективен для материалов с высокой электропроводностью, обеспечивающей низкие тепловые потери и достаточно высокий КПД.
2. Диэлектрические материалы данным методом не обрабатываются, так как они прозрачны для магнитного поля. Поэтому камеры для обработки удобно изготавливать из пластмасс или стекол.
3. Толщина заготовки должна быть больше глубины проникновения магнитного поля в материал заготовки, но не слишком большой для данного значения электромагнитных сил.
4. Поскольку инструментом является магнитное поле, то отсутствует механическое сопротивление с деталью, что позволяет обрабатывать заготовки с защитно-декоративными покрытиями.
5. Благодаря высоким скоростям обработки и наличию значительного выделения тепла в заготовке возможна обработка твердых и маловязких материалов - материалов, не обладающих достаточной пластичностью при обычных скоростях и температурах.
6. Значительная часть энергии превращается в тепло в зарядной и разрядной цепях, в самой заготовке. Поэтому КПД процесса низкий и составляет 10-40 %, он зависит от материала заготовки (плотности, электропроводности) и соотношения габаритов (радиуса и толщины).
Инструмент для магнитно-импульсной обработки.
Рабочим инструментом для магнитно-импульсной обработки является индуктор. Индукторы бывают однократного и многократного использования.
Индукторы однократного использования применяют в единичном производстве, они разрушаются под действием первого импульса магнитного поля, поэтому не должны обладать повышенной прочностью, а должны быть просты в изготовлении и дешевы. Они представляют собой обычно один или несколько витков изолированной проволоки или шины.
Индукторы многократного использования бывают одновитковые, многовитковые и представляют собой спирали, изолированные от корпуса. Одновитковые Индукторы обладают высокой механической прочностью, но они не позволяют получить высокую индукцию. Многовитковые индукторы более эффективны в работе, но они сложнее в изготовлении и дороже. Так как индукторы многократного использования подвергаются ударным нагрузкам, то они должны обладать высокой механической прочностью. Поскольку у них должна быть и высокая электропроводность в поверхностном слое, то их изготавливают из стали, плакированной материалом с высокой электропроводностью.
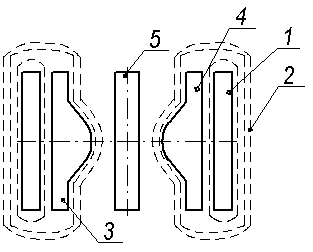 |
Рис. 6.9. Схема концентрирования магнитного поля |
Для увеличения прочности индукторов и для придания им универсальности служат концентраторы магнитного поля, помещенные внутрь индуктора. Концентратор магнитного поля представляет собой толстенную втулку из высокопрочного материала, обладающего хорошей электропроводностью (например, из бериллиевой бронзы), с разрезом вдоль образующей, заполненным изоляцией, для предотвращения образования вихревых токов. По площади заготовки магнитное поле может быть равномерным или сконцентрированным на определенном участке с помощью металлических концентраторов, изменяющих плотность магнитных силовых линий.
На рис. 6.9 показана схема концентрирования магнитного поля.
Концентрирование магнитных силовых линий (1), созданных индуктором (2) в области (3) концентратором (4) и заготовкой (5).
В реальных установках для деформации заготовок необходимы импульсные магнитные поля 2 105-106 Гс, которые позволяют получить давление 3 103 - 4 104 кГ/см2.
Длительность импульса при этом должна быть 10-20 мкс.
Штамповка с помощью импульсных магнитных полей.
Магнитно-импульсная обработка материалов и сплавов занимает видное место среди импульсных высокоэнергетических методов металлообработки. Штамповка из плоских и трубчатых заготовок нашла широкое применение. По сравнению с другими методами штамповки магнитно-импульсная штамповка обладает рядом существенных преимуществ, основными из которых являются:
а) большая скорость изменения формы обрабатываемого материала,
б) возможность точного регулирования параметров процесса,
в) возможность широко автоматизировать операции процесса,
г) высокая производительность.
Данный метод пригоден для обработки различных металлов и сплавов, но наибольшее применение он нашел для металлов и сплавов с высокой электропроводностью (медь, алюминий и их сплавы). Это связано с тем, что у заготовок с высокой электропроводностью осуществляется прямое формообразование. Для заготовок с недостаточно высокой электропроводностью (например, углеродистые нержавеющие стали) деформирование заготовок осуществляют через передающую среду или промежуточные материалы с высокой электропроводностью ("спутники"), помещаемые на обрабатываемую заготовку.
Существуют различные схемы штамповки труб и плоских заготовок, отличающиеся формой заготовки, местом расположения индуктора ( внутри или снаружи заготовки), наличием или отсутствием эластичной передающей среды. На рис. 6.10 приведены схемы раздачи(а) и обжима (б) труб. При раздаче индуктор (1) вставляется в трубу (2), при обжиме труба находится внутри индуктора.
В обоих случаях магнитное поле создает давление, которое изменяет форму трубы по форме матрицы (3). Аналогично изменяется и форма плоских заготовок. Давление, действующее на деформируемую заготовку при ее обжиме в цилиндрическом индукторе возрастает при уменьшении поверхности, находящейся внутри индуктора, т. е. при уменьшении диаметра и длины заготовки. Максимальное значение этого давления достигается при определенном соотношении глубины проникновения поля в заготовку с ее диаметром и толщиной стенки.
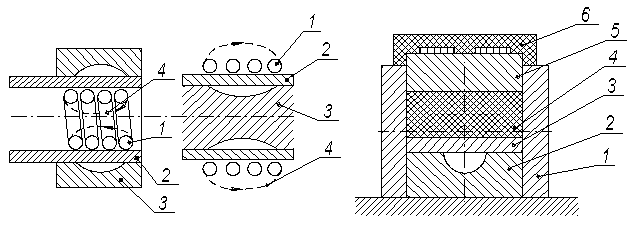 |
Рис. 6.10. Схемы раздачи и обжима труб | Рис. 6.11. Схема магнитно-импульсной магнитно-импульсным способом штамповки |
Экспериментально было получено соотношение
устанавливающее математическую зависимость между изменением диаметра заготовки Д, импульсом давления Р, временем его действия τ, шириной формующего участка М, толщиной заготовки η и плотностью материала заготовки d. Здесь к - коэффициент пропорциональности.
На рис. 6.11 приведена схема магнитно-импульсной штамповки листового металла через эластичную передающую среду. При данном методе штамповки в толстостенный контейнер 1 помещают металлическую матрицу 2, затем заготовку 3, на которую укладывают блок из эластичного материала 4. Этот блок закрывается подвижной пластиной 5, представляющей комбинацию из электропроводного материала(алюминия, меди и т.д. ) со стороны индуктора 6 и стали или высокопрочного сплава со стороны пластичного материала.
Давление, создаваемое импульсным магнитным полем через подвижную пластину передается на пластичный материал, который вдавливает заготовку в углубление матрицы. В качестве материала для эластичных блоков используют резины определенных сортов и полиуретан. Кроме эластичной среды используют жидкость.
Сборочные операции, выполняемые с использованием импульсного магнитного поля.
Импульсные магнитные поля позволяют производить соединение деталей, которое отличается от механических способов рядом преимуществ.
1. Можно соединять трубчатые детали с деталями самой различной формы.
2. Исключается опасность повреждения наружной поверхности из-за отсутствия соприкосновения детали с инструментом.
3. Процесс сборки легко поддается автоматизации.
4. Качество сборки не зависит от квалификации оператора. Наиболее распространенной операцией сборки деталей является соединение двух трубчатых деталей обжимом наружной трубы по внутренней стороне или соединение трубчатой детали со стержнем таким же способом. Этот способ позволяет соединять детали из разных материалов, что невозможно или затруднено выполнить методом обычной сварки. Повышение прочности соединения достигают нарезанием кольцевых канавок на внутренней или обеих деталях.
Другой областью применения магнитно-импульсного метода является напрессовка и пайка наконечников на концы кабелей. Алюминиевые проводники под действием высокого давления деформируются, принимая шестигранную форму. Если проводники предварительно облужены, то одновременно с опрессовкой может производиться пайка наконечника с кабелем.
Прочность соединения методом обжима зависит от величины зазора между деталями и от шероховатости поверхностей. Величина зазора, обеспечивающего максимальную прочность составляет примерно 0,3 мм, при больших и меньших его значениях прочность соединений уменьшается. С ростом шероховатости в диапазоне 10-49 мкм прочность соединения увеличивается.
Магнитно-импульсным методом осуществляют напрессовку алюминиевых наконечников на фарфоровые изоляторы. Поскольку в такой технологии легко контролировать и поддерживать на необходимом уровне ударную нагрузку, то операции осуществляют без повреждения хрупкого фарфора.
Данный метод применяют для опрессовки шлангов высокого давления, опрессовки наконечников на канаты, соединения проводов трубкой. Широкое распространение получила сварка деталей магнитно-импульсным способом. Этот вид сварки похож на холодную сварку давлением, так как в структуре сварного соединения отсутствуют деформации поверхностных слоев в свариваемых деталях.
Такая сварка применяется при изготовлении теплообменных аппаратов, где необходимо соединять трубы между собой или трубы с трубными решетками, выполненными из разнородных металлов. Прочность сварного соединения также как и при обжиме возрастает с увеличением шероховатости поверхности.
Другой возможной областью применения магнитно-импульсной сварки является ядерная энергетика: приварка заглушек из сплава, плохо поддающегося сварке обычными методами, к оболочкам топливных элементов из сплавов с большим электрическим сопротивлением R= 3 мкОм/см у сплава SАР, R = 74 мкОм/см - у сплава "циркалой -2". Результаты исследования структуры и механических свойств сварного соединения сплава "циркалой-2" показали, что изменений твердости не происходит, а испытания на растяжение и сжатие, выполняемые при 733 К и скорости деформирования 0,2 мм/мин, показали преимущества магнитно-импульсной сварки по сравнению с электросваркой.
Возможна диффузионная сварка энергией магнитного поля, Процесс сварки состоит из двух стадий:
- индукционного нагрева соединенных деталей,
- последующего сжатия деталей магнитным полем. Частота тока зависит от толщины деталей. Так, для плакирования труб с толщиной стенки 0,6 мм, менее 5 мм и более 5мм оптимальная частота тока составляет 450, 10 и 1-3 кГц соответственно.
Электроэрозийная обработка материалов
6.11Физические основы электроэрозийной обработки
История развития электроэрозийной обработки.
Электрическая эрозия является вредным явлением, возникающим на различных контактах электрических устройств - реле, рубильников, выключателей. Она приводит к разрушению контактов и сокращению их сроков службы. Поэтому много исследований было посвящено изучению этого явления и разработке способов борьбы с ним.
В годы II мировой войны над этой проблемой работали советские ученые Б.Р. Лазаренко и Н. И. Лазаренко. Они, изучая явление электрической эрозии металлов, пришли к заключению, что его можно использовать для обработки материалов. Это изобретение имело выдающееся значение в технике обработки материалов, поскольку к традиционным методам механической обработки (резанию, шлифованию, сверлению) добавлялся новый метод, основанный на явлениях в электрических разрядах. Авторы изобретения были удостоены Государственной премии СССР.
В последующие годы электроэрозийная обработка успешно развивалась, схемы усовершенствовались, показатели улучшались. В этом большая заслуга принадлежит отечественным ученым и инженерам Б. Н. Золотых, А. Л. Лившицу, Л. С. Палатнику и другим.
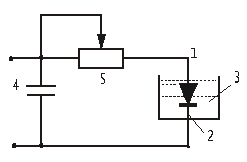 |
Рис. 6.12 Схема установки Лазаренко Б. Р. |
Схема первой экспериментальной электроэрозийной установки Лазаренко Б. Р. и Лазаренко Н. И. показана на рис. 6.12. На помещенные в жидкий диэлектрик 1 электрод 2, являющийся инструментом, и электрод 3, являющийся обрабатываемой деталью, подавался импульс напряжения от конденсатора 4. Зарядку конденсатора осуществляли от источника постоянного напряжения, время зарядки регулировали реостатом 5.
Принцип работы схемы заключается в следующем. При подаче импульса тока на электроды 2 и 3 между ними создается электрическое поле, напряженность которого зависит от межэлектродного расстояния. При сближении электродов между ними возникает разряд, который приводит к разрушению материала заготовки детали. Капли металла охлаждаются диэлектрической жидкостью и в виде шариков удаляются из межэлектродного промежутка. Таким образом, основными элементами первой схемы ЭЭО были: генератор импульсов, конденсатор, реостат, источник напряжения, электрод - инструмент, обрабатываемая деталь и жидкий диэлектрик.
Физические процессы при электроэрозийной обработке
Удаление металла с заготовки осуществляется за счет микроразрядов, возникающих в среде диэлектрика между инструментом и заготовкой и разогревающих их поверхностные слои. Эти - процессы происходят при сближении электрода - инструмента и заготовки, в результате чего напряженность поля Е увеличивается по закону.
где U - напряжение между электродами,
d - расстояние между электродами.
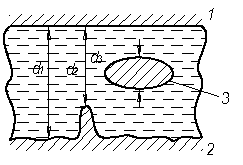 |
Рис. 6.13. Схема расположения инструмента (1), заготовки (2) и токопроводящего включения (3); d1-наибольшее расстояние; d2 -наименьшее расстояние; d3-размер включения. |
Наибольшая напряженность возникает на тех участках, где имеются выступы или где в зазоре находятся какие-либо проводящие включения. На рис. 6.13 показана схема расположения инструмента, заготовки и диэлектрического промежутка. Наибольшее расстояние между электродом-инструментом 1 и заготовкой 2 равно d1 наименьшее d2. За счет токопроводящего включения 3 расстояние d1 уменьшается на величину d3.
При сближении электродов до величины зазора, равного критическому, происходит пробой межэлектродного промежутка и возникает электрический разряд. Металл заготовки нагревается за счет бомбардировки его частицами разряда.
Если заготовка является анодом, то она бомбардируется электронами, а на электрод - инструмент движутся ионы. Поскольку скорость движения этих частиц при одинаковом напряжении определяется их массой, согласно выражения
где m, V, q - масса, скорость и заряд заряженной частицы, соответственно, U - ускоряющее напряжение, то электроны будут достигать поверхности заготовки быстрее, чем ионы достигнут поверхности электрода - инструмента.
Электроны будут разогревать поверхность заготовки, и расплавленный металл будет вылетать из заготовки, охлаждаться диэлектрической жидкостью в зазоре и в виде шариков удаляться вместе с жидкостью из зазора. В результате образуется углубление в виде лунки. Затем пробой возникает в другом месте, где расстояние достигает критического значения dкр и там происходит удаление металла. Таким образом происходит выравнивание поверхности заготовки и удаление металла.
Для того чтобы меньше разрушался электрод - инструмент при подаче на него отрицательного напряжения (прямое включение полярности) необходимо подбирать такую длительность импульса, при которой ионы не будут успевать достигать катода за время действия импульса. Такой способ обработки называется электроискровым,
Но при малой длительности импульса скорость обработки будет уменьшаться, уменьшаться будет и производительность. Поэтому длительность импульса подбирают такой, чтобы и скорость обработки была достаточной и износ электрода - инструмента был мал.
Если необходимо иметь большие скорости съема материала заготовки, то следует увеличивать длительность импульса и поменять полярность: положительный потенциал подать на инструмент, отрицательный - на заготовку. Тогда под действием ионов разряда интенсивно будет разрушаться заготовка, а на инструмент будут идти электроны. Такая схема включения будет называться электроимпульсной обработкой.
При электроэрозийной обработке напряжение составляет 40-180В в электроискровом способе и 18-136В - в электроимпульсном способе. Напряженность поля в межэлектродном промежутке в момент пробоя достигает 107В/м, в зоне разряда образуется плазма, скорость нарастания тока в которой составляет 105А/с. Длительность импульса тока при черновой обработке деталей составляет от 200 до 105 мкс, а при чистовой -от 5 до 200 мкс. Величина тока достигает от 20 до 100 А при черновой и от 0,5 до 50 А при чистовой обработке соответственно.
Основные стадии и закономерности электроэрозийной обработки
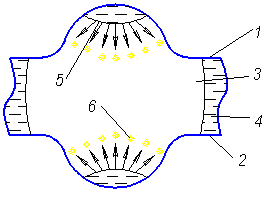 |
Рис. 6.14. Схема третьей стадии электроэрозийного процесса: 1, 2 - электроды; 3 - газовый пузырь; 4 - сжатая жидкость; 5 - лунка; 6 - расплавленный металл. |
Можно выделить три стадии электроэрозийного процесса:
I. Нагрев, оплавление металла, образование лунки.
II. Образование газового пузыря из паров металла и жидкости.
III. Расширение газового пузыря, отрыв ударной волны от газового пузыря и ее гашение жидкостью.
После нагрева, оплавления металла и образования лунки, наступает вторая стадия эрозийного процесса - образование газового пузыря из паров металлов и жидкости. В канале проводимости, образованном в месте возникновения микроразряда, создается высокое давление, достигающее значений 2∙107 Па. Канал проводимости расширяется, образуется газовый пузырь, который сжимает окружающую газовую фазу. Граница пузыря движется с высокой скоростью, достигающей 22 м/с. Между газовым пузырем и окружающей жидкостью образуется фронт уплотнения, в котором давление скачкообразно меняется от исходного в жидкости до 107Па.
Третья стадия процесса характеризуется прекращением тока между электродами, расширением газового пузыря, отрывом ударной волны от газового пузыря и гашением ее жидкостью. При расширении пузыря давление в нем резко падает и содержащийся в лунках расплавленный металл выбрасывается в межэлектродный промежуток и застывает в виде шариков. Схема третьей стадии показана на рис. 6.14.
Между электродами 1 и 2 образуется газовый пузырь 3, который, расширяясь, сжимает жидкость 4. Из лунки 5 расплавленный металл 6 в виде шариков выбрасывается в межэлектродный
В качестве жидкостей используют различные диэлектрики: масла, керосин, выполняет двоякую роль - роль диэлектрического промежутка и роль охлаждающей среды. Кроме того, она уносит продукты обработки. Поэтому жидкость прокачивается через промежуток с определенной скоростью. Если же скорость обработки мала, то емкость с жидкостью делают соответствующего объема и жидкость не прокачивается.
Если электроэрозийную обработку проводят в воздушной среде, то вместо электроискрового разряда возникает более длительный электродуговой разряд, поскольку охлаждение менее интенсивное, чем в жидкости. Такой способ обработки называется электроконтактным. Схема электроконтактной обработки показана на рис. 6.15.
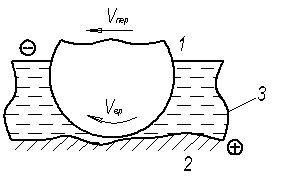 |
Рис. 6.15. Схема электроконтактной обработки: 1-инструмент; 2-деталь; 3-диэлектрик; Vпер-скорость перемещения; Vвр-скорость вращения инструмента. |
Между электродом - инструментом 1 и деталью 2 находится диэлектрик. Поверхности электродов имеют выступы и не являются идеально гладкими. Поэтому при сближении до определенного значения dкр возникает разряд. Если обработка ведется в воздушной среде, то возникают длительные дуговые разряды. Выплавляются большие участки заготовки. Поскольку зазор между электродами в такой схеме обработки мал, то возможен вариант не только съема металла, но и наращивания материала инструмента на заготовке за счет попадания расплавленного материала инструмента и его застывания на заготовке. Этот процесс называется электроэрозийным легированием.
При электроконтактной обработке напряжение на электродах обычно составляет 1- 2 В и достигает до 12В в воздушной среде и от 8 до 40В в жидкой среде. Существуют три источника тепла, вклад которых зависит от напряжения и скорости вращения электрода-инструмента: механический, дуговой и электрический. Механический определяется скоростью вращения электрода-инструмента, дуговой - напряжением, током и длительностью дугового разряда, электрический сопротивлением в местах электрического контакта.
При электроконтактной обработке при малых напряжениях (1-2) В основной вклад в нагрев дает трение, при напряжении порядка 10В нагрев идет, в основном, за счет дугового разряда.
Выбрасывание расплавленного металла в электроконтактном способе осуществляется подвижным электродом-инструментом, который помимо вращения перемещается по поверхности заготовки.
Большим достоинством электроконтактного способа является возможность осуществления легирования заготовки и ее упрочнения. Поскольку: материал электрода-инструмента (анода) не переносится на заготовку (катод), то происходит их взаимодействие и образование новых сплавов в поверхностном слое. При этом образуются нитриды или карбиды - слои с высокой износостойкостью. Происходит также диффузия материала анода в более глубокие слои заготовки.
Материалы для электрода-инструмента.
Критериями выбора материалов для электрода-инструмента
- эрозийная стойкость,
- удельная проводимость,
- прочность,
- коррозийная стойкость,
- возможность изготовления инструмента требуемой формы с минимальными затратами, - стоимость.
По эрозийной стойкости, в порядке ее возрастания, материалы можно расположить в ряд: алюминий и его сплавы, серый чугун, латунь, медь, вольфрам, графитовые материалы.
Эрозия материала зависит от теплопроводности и температуры плавления. При постоянной энергии импульса нагрев тем меньше, чем больше теплопроводность, так как тепло быстрее уходит внутрь материала. Поэтому электроды-инструменты выполняют обычно из меди, латуни, алюминия, поскольку их эрозия меньше, чем эрозия твердых сплавов и стали. В то же время материал должен иметь высокую температуру плавления. Поэтому для изготовления электрода-инструмента иногда применяют графит, вольфрам, композиции меди и вольфрама. Чаще же применяют электроды из меди и латуни, так как они более дешевы и могут быть изготовлены любой формы.
Наиболее интересным решением вопроса о повышении износостойкости инструмента является процесс нанесения (осаждения) на поверхности слоя углерода, образующегося в результате разложения углеродосодержащей рабочей жидкости. При равенстве скоростей износа и осаждения слоя форма и размеры инструмента будут постоянными в процессе работы. Этого можно достичь подбором особой формы импульса напряжения: с крутым передним фронтом, необходимым для обеспечения разряда и гребенчатым задним фронтом, необходимым для разложения рабочей жидкости и выделения углерода. Примером является такое осаждение углерода на медь. Износостойкость повышается в десятки раз.
Тепловые процессы при электроэрозийной обработке
Приближенный расчет температуры в окрестности разряда производят при следующих предположениях:
- разряд является стационарным источником теплоты,
- теплофизические характеристики электродов и межэлектродного промежутка являются постоянными во времени.
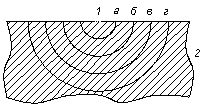 |
Рис. 6.16. Схема распространения тепла в материале заготовки: 1-точечный источник тепла; 2-заготовка. |
Схема распространенна теплоты в материале заготовки показана на рис. 6.16.
Точечный источник тепла 1 излучает энергию во все стороны, но большая ее часть из-за малых размеров попадает на электрод - заготовку 2. Изменение температуры заготовки определяется выражением:
где Q - безразмерный параметр температуры, учитывающий теплопроводность заготовки λ и время действия импульса энергии τ;
Р - энергия импульса;
с - удельная теплоемкость материала заготовки;
ρ
- плотность материала заготовки;
r - расстояние от источника тепла до точки определения температуры;
η - коэффициент полезного действия импульса энергии.
Коэффициент полезного действия импульса энергии определяется выражением:
где к1 - коэффициент, учитывающий потери энергии на нагрев жидкости, образование газового пузыря и ударной волны и равный 0,5 при электроискровом режиме и 0,47 при электроимпульсном режиме;
к2 - коэффициент, учитывающий нагрев электрода-инструмента и зависящий от его теплофизических характеристик и расположения относительно заготовки;
к3 - коэффициент, характеризующий свойства диэлектрической среды, изменяющийся от 0,2 (керосин) до нуля (масла);
к4 - коэффициент, учитывающий изменение напряжения, равный +0,1, если напряжение выше номинального и -0,1, если напряжение ниже нормального.
В качестве примера в табл. 1-1 показана зависимость температуры металла от расстояния от точечного источника по сферическим кривым (изотермы) в конце действия импульса мощностью 0,54 Дж длительностью 8мс.
Таблица 6.2 Зависимость температуры металла от расстояния от точечного источника тепла
г, мкм | 0 | 5 | 10 | 15 | 20 | 30 | 40 | 50 |
Т, К | 5700 | 4850 | 3350 | 2870 | 1850 | 630 | 335 | 296 |
Температура плавления металла равна 1850 К, перегрев до температуры 5700 К необходим для обеспечения его жидкотекучести при выбрасывании из лунки. Глубина лунки при этих условиях составляет 20 мкм.
6.12 Технологические процессы изготовления деталей и показатели ЭЭО
Схемы электроэрозийной обработки.
Технологические схемы электроэрозийной обработки, используемые в промышленности, следующие:
а) прошивание отверстий,
б) разрезание,
в) электроэрозийное шлифование,
г) электроэрозийное упрочнение.
Прошивание - это удаление металла из полостей, углублений, отверстий, пазов. Существует два вида прошивания:
- прямое копирование, когда инструмент расположен над заготовкой;
- обратное копирование, когда инструмент расположен под заготовкой.
Во втором случае облегчается удаление продуктов обработки. Разрезание профильным или непрофильньгм инструментом предполагает разделение заготовки на части - отрезание, или получение непрямолинейного контура - вырезание. Отрезание выполняется пластиной или диском. В обоих случаях инструмент перемещается к заготовке, но диск дополнительно еще вращается.
Электроэрозийное шлифование выполняется с помощью диска, совершающего вращательное и поступательное движения. При этом заготовка может быть неподвижной или вращающейся. Если вращение происходит в одну сторону, шлифование называется попутным, если в разные стороны - встречным.
Электроэрозийное упрочнение происходит как за счет легирования, так и за счет наращивания поверхности. Оно обычно осуществляется при электроконтакт
ном способе, поэтому будет более подробно рассматриваться далее.
Прошивание отверстий и полостей.
Схема электроэрозийного прошивания отверстий и полостей показана на рис. 6.17. Между электродом-инструментом 1 и заготовкой 2 подается напряжение и возникает электрический разряд. В ванной 3 электролитом 4 выносятся продукты обработки 5 в виде шариков.
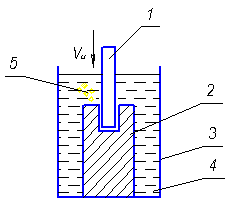 |
Рис. 6.17. Схема прошивания отверстий и полостей: 1-электрод-инструмент; 2-заготовка; 3-ванна; 4-электролит; 5-продукты обработки; Vu-скорость подачи инструмента. |
Операции прошивания применяются во многих случаях.
1) Удаление из обрабатываемых деталей обломков метчиков, сверл и других инструментов. В таких случаях используют схему прямого копирования. Для электрода-инструмента применяют медь, латунь, алюминий или его сплавы. Электроэрозийный способ удаления обломков инструмента и крепежа применяется на заключительных операциях, позволяет устранить брак технологического процесса, исключить необходимость отжига детали, который применяют для снижения твердости обломков инструмента.
2) Изготовление деталей из труднообрабатываемых материалов, таких как жаропрочные сплавы, закаленные детали, магнитные сплавы. Для выполнения таких операций производят расчеты режимов обработки (энергию импульса, напряжение холостого хода, длительность обработки, производительность), исходя из условий шероховатости отверстия.
Материалом электрода-инструмента являются графитовые композиции при обработке закаленных, жаропрочных и твердых сталей; при обработке титановых сплавов применяют латунь. Обычно такие операции производят без прокачки рабочей жидкости, но для повышения точности обработки производят прокачку или отсос жидкости.
При прошивании глубоких отверстий возникают трудности, связанные с поддержанием необходимых режимов при значительном внедрении электрода-инструмента в заготовку, так как при этом резко возрастает вибрация инструмента, затруднено удаление продуктов обработки из отверстия.
Конструкция электрода-инструмента зависит от отношения глубины отверстия е к его диаметру d. При е/d<=20 и d<5мм, l<=100мм можно использовать сплошной стержень, но при этом производительность обработки по мере углубления электрода-инструмента в деталь снижается на 10-15 %, При l/d>20 применяют электроды-инструменты в виде трубки из меди, латуни, графитовых материалов. Отверстия позволяют прокачивать или отсасывать рабочую жидкость и сократить время обработки за счет устранения периодического выведения инструмента из углубления. Такая конструкция позволяет получать глубокие отверстия с соотношением l/d=40. Если требуется получить отверстия с l/d>40, то применяют трубки с нарезным спиральным каналом для удаления продуктов обработки, иногда используют вращение инструмента.
3) Прошивание некруглых отверстий и пазов проводят очень часто в тех случаях, когда необходимо такой профиль получать на твердых сплавах. Например, при изготовлении лопаток турбин авиационных двигателей, при изготовлении матриц и штампов, изготовлении каналов и пазов в насосах, турбинах, компрессорах. Электрод-инструмент в таких случаях изготавливают из меди, латуни, чугуна или графитовой сплава. Если профиль отверстия сложный и по длине непрямолинейный то предусматривают поворот электрода-инструмента в процессе обработки.
4) Прошивание соединительных каналов в корпусах гидроаппаратуры трудно выполнимо методами механической обработки. Если же поперечное сечение каналов некруглое, то его получение возможно только с применением электрических методов, в частности электроэрозийным прошиванием.
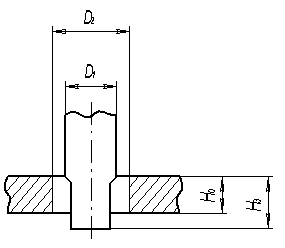 |
Рис. 6.18. Схема сквозной обработки цилиндрического отверстия |
Расчет размеров электрода-инструмента для обработки сквозных или глухих отверстий различной формы приведен в специальной справочной литературе. Здесь мы рассмотрим наиболее простые формы отверстии и формулы для расчета размеров электрода-инструмента.
На рис. 6.18 приведена схема сквозной обработки цилиндрического отверстия.
Здесь обозначено Do, Но - диаметр отверстия и его глубина соответственно, Dэ - размер рабочей части электрода-инструмента в горизонтальной плоскости; Нрэ -длина рабочей части электрода-инструмента.
При такой схеме обработки при однопроходном прошивании отверстий размеры электрода-инструмента определяются выражением:
где l - боковой межэлектродный зазор, равный 0,35 ÷ 1,48 мм в зависимости от значения максимального тока обработки в импульсе, изменяющегося в пределах 50 - 300 А;
γэ - относительный износ электрода-инструмента, зависящий от его материала (медь, чугун графитированный), формы и частоты импульсов, материала заготовки.
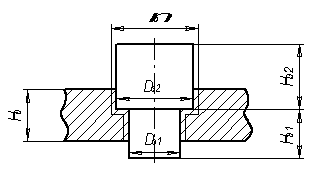 |
Рис. 6.19. Схема сквозной обработки отверстия ступенчатой формы. |
Например, при f=22 кГц прямоугольных, импульсах е графитированном электроде, при обработке стали, γэ= 3 - 5%; при гребенчатой форме импульсов и тех же параметрах γэ= 0,08 - 0,15%. Если отверстие ступенчатой формы, то формулы для расчета размеров электрода инструмента усложняются (рис. 6.19).
Здесь Δ - допуск на размер отверстия в горизонтальной плоскости;
lτ - торцевой межэлектродный зазор, зависящий от частоты, формы и тока импульсов и изменяющийся от 0,01 до 0,5 мм.
Помимо рассмотренных выше операций, большое место занимают прошивание наружных поверхностей, изготовление сеток, решеток, тонкостенных деталей конструкций, а также маркирование деталей.
Электроэрозийное шлифование.
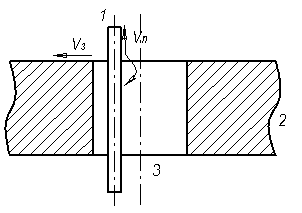 |
Рис. 6.20. Схема шлифования проволочным электродом: 1-электрод-инструмент; 2-заготовка; 3-отверстие; Vп, Vз- скорость подачи и скорость перемещения проволоки и детали соответственно. |
Электроэрозийное шлифование применяют для обработки магнитных слитков, электротехнических изделий, собранных из тонких пластин. Преимущество электроэрозийного шлифования перед механическим заключается в том, что отсутствуют большие нагрузки, исключается скалывание твердосплавных и магнитных материалов.
Для шлифования мелких отверстий, например, в твердосплавных фильтрах применяют проволочный электрод, который постоянно протягивается, что исключает влияние его износа на точность обработки. Схема такого шлифования показана на рис. 6.20.
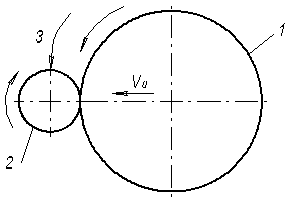 |
Рис. 6.21 Схема встречного шлифования: 1-электрод-инструмент; 2-заготовка; 3-сопло полива жидкостью; VU-скорость подачи инструмента. |
Электрод-инструмент (проволока) 1 вводится в заготовку 2 через предварительно вскрытое отверстие 3. Вращение и передвижение(V3) к стенке отверстия приводит к шлифованию, а передвижение (Vu) проволоки позволяет избежать износа инструмента.
Помимо шлифования проволочным электродом применяется встречное шлифование, схема которого показана на рис. 6.21. В этом случае электрод-инструмент 1, изготовленный в виде диска, и заготовка 2 вращаются в противоположных направлениях. Заготовка поливается рабочей жидкостью, подаваемой через сопло 3. Электрод-инструмент подается с постоянной скоростью Vи к заготовке по мере ее обработки.
Электроэрозийное разрезание заготовок.
Разрезание заготовок электроэрозийным способом осуществляют диском или лентой. При разрезании диском заготовка может быть неподвижной или вращающейся. Вращение позволяет повысить производительность в 3 - 4 раза. Если вращения нет, то целесообразно при разрезании толстых заготовок (более 100 мм) заготовку перевернуть после прохождения середины и дальнейшие операции производить с обратной стороны.
Процесс ведут на воздухе или в жидкой среде при токе 600, 800 А. Диск выполняется из листовой стали до 1 мм толщиной и до 1000 мм диаметром. Погрешность достигается не более 0,2 - 0,3 мм. Если разрезается жаропрочная сталь, то время сокращается в 8 -10 раз по сравнению с механическим разрезанием. При разрезании лентой ее толщина небольшая и значительно уменьшить толщину реза. Применяют латунные ленты толщиной 0,1 мм и стальные толщиной 0,3мм. Схема разрезания показана на рис. 6.21. Электроэрозийное разрезание используют в основном производстве для разделения нежестких заготовок, например, тонкостенных трубок. В инструментальном производстве этим методом отрезают заготовки для резцов, штампов из твердосплавных материалов. При изготовлении вырубных штампов фильер, матриц использую!
Электроэрозийное упрочнение деталей
Поскольку в электрическом разряде осуществляется перенос металла, то электроэрозийным методом возможно упрочнение деталей. Оно может быть нескольких видов:
- наращивание значительного слоя металла с целью упрочнения и восстановления изношенных участков деталей;
- нанесение тонких покрытий из благородных металлов, например, для электрических контактов;
- упрочнение за счет изменения физико-механических свойств поверхности без изменения размеров детали.
Современное оборудование для упрочнения позволяет проводить операции в различных режимах - "грубые", "черновые" и "чистовые".
Производительность электроэрозийной обработки.
Производительность электроэрозийной обработки определяется отношением массы или объема удаленного металла ко времени обработки и выражается в граммах/с или мм3/с. Она пропорциональна мощности, расходованной в межэлектродном промежутке.
где С - коэффициент, зависящий от теплофизических характеристик материала;
Р - мощность;
А - энергия в импульсе;
f - частота следования импульсов.
Если же производить отрезание заготовки электроэрозийным методом, то такое определение производительности будет неправомерным, поскольку масса снятого материала в этом случае не является критерием операции. Площадь боковой поверхности реза в этом случае является мерой выполненной операции, а ее отношение ко времени обработки - производительностью (S/t). Площадь определяется произведением толщины заготовки на длину реза или площадью круга для круглых заготовок. Производительность легирования с целью упрочнения материала определяется отношением площади нанесенного слоя ко времени обработки:
В любом случае производительность зависит от мощности, реализуемой в межэлектродном промежутке. С увеличением мощности увеличивается скорость обработки, но при этом увеличивается и количество продуктов обработки, которые тормозят процесс съема металла. По мере углубления в заготовку, усложняется удаление продуктов обработки и поступление свежей жидкости в межэлектродный промежуток. В межэлектродном промежутке образуется большое количество электропроводных капель застывшего металла и энергия тратится на вторичное расплавление этих частиц. Для их удаления и повышения производительности используют принудительную прокачку рабочей жидкости.
В зависимости от свойств рабочей среды изменяется доля полезного использования энергии импульса. Поэтому для каждого вида обработки применяют оптимальную диэлектрическую среду: если в процессе электроэрозийной обработки используется малая энергия импульса, то применяют дистиллированную и техническую воду или керосин, при больших энергиях импульса применяют масла, дизельное топливо, т. е. тяжелые фракции нефти. На рис. 6.22 показано влияние состава среды на производительность обработки при прошивке медно-графитовым электродом ферросилида. Видно, что из трех видов диэлектрической жидкости наибольшая производительность достигается при обработке в керосине, наименьшая - при обработке в воде.
Для сравнения эффективности электроэрозийной обработки различных металлов и сплавов введено понятие обрабатываемости, которое определяется отношением массы снятого металла к массе металла, снятого с заготовки стали 45.
Точность ЭЭО.
Под точностью электроэрозийной обработки понимается степень соответствия формы и размеров детали чертежу. Отклонение от формы и размеров называется погрешностью.
На точность ЭЭО влияют:
- точность изготовления электрода-инструмента;
- износ электрода-инструмента;
- погрешность формы и размеров углубления на заготовке относительно электрода-инструмента, зависящая от нестабильности режимов обработки, вызванной колебаниями напряжения в сети, изменениями скорости подачи и износом электрода-инструмента.
Износ электрода-инструмента является основным фактором, влияющим на точность обработки. Для большинства режимов обработка он составляет:
- при прошивании сталей в электроискровом режиме медным электродами 30 - 95% от объема снятого металла с заготовки;
- при работе в электроимпульсном режиме медно - графитовым электродами 0,1 - 4%;
- при электроконтактном резании на воздухе до 30%.
Для снижения влияния износа на точность обработки необходимо:
а) изготавливать электрод-инструмент из стойкого к эрозии:
материала (из вольфрама, меднографита и др.);
б) использовать безизносные схемы, в которых часть материала и рабочей среды осаждают на электроде-инструменте, компенсируя тем самым его износ;
в) заменять изношенные участки электрода-инструмента путем его перемещения.
Погрешность при электроэрозийном легировании определяете неравномерностью наносимого слоя и достигает 20% от его толщины.
6.13 Электроэрозийное оборудование
Компоновка оборудования.
Станки для электроэрозийной обработки включают - следующие блоки системы:
- генераторы импульсов,
- средства регулирования и управления,
- систему подачи и очистки рабочей жидкости.
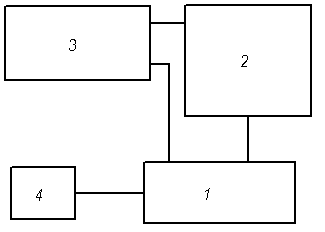 |
Рис. 6.23. Блок-схема электроэрозийного станка |
Блок - схема электроэрозийного станка показана на рис. 6.23. Она включает: механическую часть (1), состоящую из рабочего стола устройства для закрепление электрода-инструмента, системы регулирования и управления; генератор импульсов (2) электрошкаф (3) с размещенными в нем пускателями, рубильниками, предохранителями; ванну с рабочей жидкостью, насосами, фильтрами (4). Электроэрозийное оборудование выпускается или серийно, или по индивидуальным заказам. Он может быть универсальным, специализированным, специальным.
Генераторы импульсов
В настоящее время известно несколько типов генераторов импульсов: релаксационные, машинные, ламповые, полупроводниковые. Основное требование к генераторам - получение импульсов необходимой формы и мощности. Хронологически первыми были релаксационные генераторы, разработанные Б. Р. Лазаренко и Н. И. Лазаренко. Параметры импульса в этих генераторах определяются состоянием межэлектродного промежутка. На рис. 6.24 показаны 4 типа RС - генераторов. Это RС (а), RLС (б), RCL (в), LС (г) - генераторы. Все релаксационные генераторы имеют зарядную и разрядную цепь. Зарядная цепь включает источник питания ИП, ключ К, токоограничивающий резистор К (в LС - генераторах его нет). Разрядная цепь состоит из межэлектродного промежутка МЭП, конденсатора С и, возможно, индуктивного элемента L.
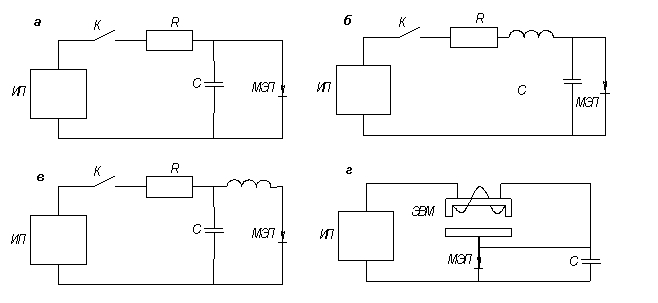 |
Рис. 6.24. Схема RC-генераторов различных типов: а-RC, б-RLC, в-RCL, г-LC |
Принцип работы всех RС - генераторов заключается в зарядке конденсатора до напряжения и от источника питания при замыкании ключа. Постоянная зарядки τ определяется произведением RС. При достижении U, равного пробивному Uпроб, происходит пробой промежутка, электроэрозийный процесс и разрядка конденсатора.
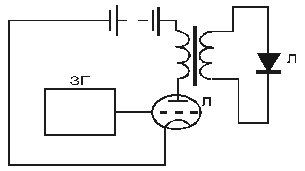 |
Рис. 6.25. Схема лампового генератора импульсов. |
Ток через промежуток прекращается, происходит процесс деионизации промежутка (восстановление диэлектрических свойств среды) и зарядка конденсатора. Необходимо, чтобы время зарядки было больше период деионизации τ > Т и чтобы разряд не перешел в дуговой. Это достигаете подбором R и С. Если быстро сближать электроды, то время зарядки уменьшается, разряды будут происходить часто, напряжение и энергия промежутка будут малы. При совсем малых расстояниях время между разрядами будет мало и деионизация промежутка будет недостаточна. Разряд может перейти в дуговой. Таким образом, от состояния МЭП (расстояние между электродами, параметры среды) зависит режим работы генератора.
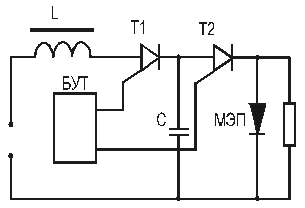 |
Рис. 6.26. Схема полупроводникового генератора импульсов |
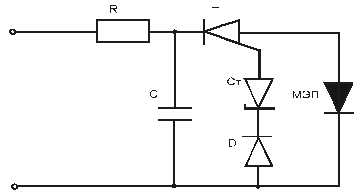 |
Рис. 6.27. Схема генератора импульсов со стабилизатором |
Обычный RС - генератор имеет малый КПД (25%) и малую мощность (5-7 кВт) из-за нагрева резистора. Повысить мощность за счет уменьшения времени зарядки и повышения напряжения удается введением L-элемента в RLС - генераторах. Но при этом, как и в RС генераторах, возникает обратная полуволна, разрушающая электрод инструмент. Этот недостаток удается устранить в RСL-генераторах. Но при этом понижается мощность. Поэтому такие генераторы используют для чистовой обработки, когда анодом служит инструмент.
С целью повышения КПД разработаны LС - генераторы, в которые исключен ограничивающий резистор, и введен электромагнитный вибратор ЭМВ, якорь которого жестко связан с электродом инструментом. При подаче напряжения ток протекает через обмотку вибратора, якорь притягивается к сердечнику и перемещает инструмент от заготовки.
В это время течет ток через конденсатор С. При достижении Ильного напряжения зарядки сердечником Umax инструмент подходит к загшотовке, промежуток пробивается, ток через конденсатор прекращается, якорь не удерживается, горит разряд, происходит электроэрозийный процесс, конденсатор разряжается. Затем процесс повторяется. Такие генераторы используются для черновой обработки.
Для повышения производительности процесса используются электронные лампы, поскольку в RС - генераторах увеличение энергии импульса связано с возрастанием времени накопления заряда. В ламповом генераторе (рис. 6.25) частота следования -импульсов определяется задающим генератором ЗГ. Частоту следования импульсов удается повысить до 20кГц. Недостатком лампового генератора является низкий КПД, высокое напряжение питания (несколько кВ).
Для получения широкой диапазона режимов обработки используются полупроводниковым генераторы импульсов. Схем генератора показана на рис. 6.26.
При подаче напряжения блок управления тиристорами (БУТ открывает тиристор Т) и ток течет через конденсатор С до его полной зарядки После зарядки БУТ закрывает тиристор Т1 и открывает тиристор Т2. В это время происходит пробой межэлектродного промежутка разрядка конденсаторе Токоограничивающим элементом является катушка индуктивности L, сопротивление Кщ в разрядной цепи позволяет разряжаться конденсатору при разомкнутом МЭП.
Недостатком таких генераторов является нестабильность напряжения пробоя, что приводит к изменению режимов обработки. Для устранения этого недостатка используют схемы со стабилитроном Ст (рис. 6.27). В ней заряд осуществляют через резистор R или катушку индуктивности. В это время тиристор Т закрыт. После зарядки напряжение на конденсаторе становится выше напряжения на стабилитроне Uс>Ucт и стабилитрон открывает тиристор. Происходит разряд со строго дозированной энергией через промежуток.
Регуляторы подачи электрода-инструмента.
Основное назначение регулятора подачи электрода-инструмента поддерживать необходимый размер межэлектродного промежутка 1 течение всего времени обработки. Поскольку величина промежутка мала (десятые доли миллиметра), то регулятор должен обладать высокой чувствительностью, быстродействием. В случае колебаний напряжения или попадания проводящих частиц в межэлектродный промежуток регулятор должен отрабатывать соответствующие команды.
Основными элементами регулятора являются:
-измерительный преобразователь,
-блок сравнения,
-усилитель,
-исполнительный механизм.
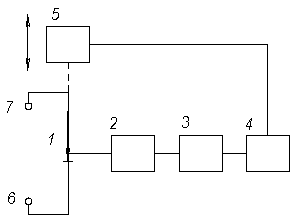 |
Рис. 6.28. Регулятор подачи электрода-инструмента: 1-МЭП; 2-измерительный преобразователь; 3-сравнения; 4-усилитель; 5-исполнительный механизм; 6,7-зажимы для генераторов импульсов. |
На рис. 6.28 показана блок-схема регулятора. Информация о зазоре из МЭП 1 поступает на измеритальный преобразователь 2, откуда в виде электрическое сигнала передается в блок сравнения 3, где происходит его сравнение с опорным сигналом
Вычитание и дальнейшее усиление в усилителе 4 Если сигнал из блока 2 больше опорного сигнала, то исполнительный механизм произведет уменьшение МЭП; если сигнал меньше опорного то исполнительный механизм увеличит зазор.
Регуляторы бывают электрогидравлические и электромеханические. У электрогидравлического регулятора исполнительным механизмом является гидропривод, у электромеханического - электродвигатель. Схема электромеханического регулятора показана на рис. 6.29.
Сигнал из МЭП 1, на который подается напряжение от генератора импульсов 2, подается на делитель напряжения 3. На него же подается и опорный сигнал из блока 4. Если они отличаются, то разностный сигнал подается на электродвигатель 5, который, вращаясь, изменяет межэлектродный промежуток. Направление вращения ЭД определяется знаком разностного сигнала. В этой схеме усилителем - преобразователем является делитель напряжения, т. е. он исполняет роль преобразователя блока сравнения и усилителя, исполнительным механизмом является электродвигатель.
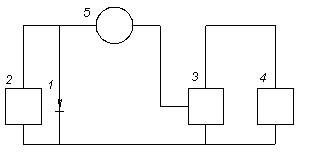 |
Рис. 6.29. Схема электромеханического регулятора: 1-МЭП; 2-генератор импульсов; 3-делитель напряжения; 4-источник опорного напряжения; 5-двигатель. |
6.13 Системы очистки и подачи рабочей жидкости
Рабочая жидкость может находиться в МЭП неподвижно между электродом - инструментом и обрабатываемой деталью или прокачиваться. При прокачке улучшается качество и точность обработки, увеличивается производительность. Для этого предназначена гидравлическая система станка. На рис. 6.30 показана схема такой системы. Из бака 1 насосами 2 через фильтры 4 и устройство регулирования расхода рабочей жидкости 5- регулятор расхода, 6-конус для сброса, 7-вентиль для сброса, подается рабочая жидкость.
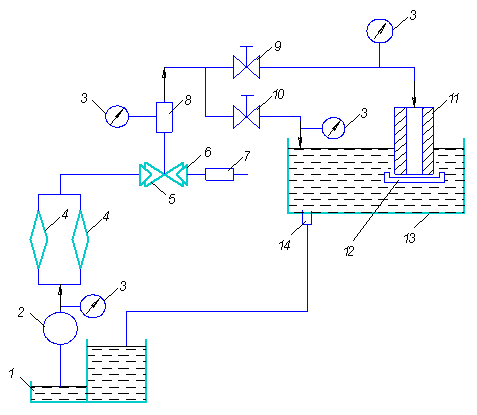 |
Рис. 6.30. Система очистки и подачи рабочей жидкости. |
При этом возникает два варианта подачи рабочей жидкости: либо Через полость электрода-инструмента 11 к детали 12 при открытом кране 9, либо через кран 10 непосредственно в рабочую ванну 13. Измерение давления осуществляется манометрами 3, слив жидкости из рабочей ванны в бак 1 осуществляется через отверстие 14. Расход жидкости измеряется ротометром 8.
Контрольные вопросы
1. Какие технологические процессы выполняются электровзрывным способом?
2. Какова величина напряжения при электрогидравлическом эффекте?
3. Как выглядит простейшая схема получения электрогидравлического эффекта?
4. Какие технологические операции выполняются магнитно-импульсным способом?
5. Каковы физические основы электроэрозионной обработки?
6. Назовите применение искрового разряда в процессах растениеводства.
|